Montreal/Berlin, 5 June 2024. The technology company Vention has analyzed in a study how companies automate their production independently. Small businesses are trendsetters in do-it-yourself (DIY) automation, but large companies are catching up. The study is based on anonymized data from over 1,400 corporate users of Vention’s Manufacturing Automation Platform (MAP) worldwide.
For the second time, Vention publishes the annual study „The State of DIY Industrial Automation“. The focus is on do-it-yourself (DIY) automation, which enables manufacturers of different sizes to automate their production independently using state-of-the-art technologies.
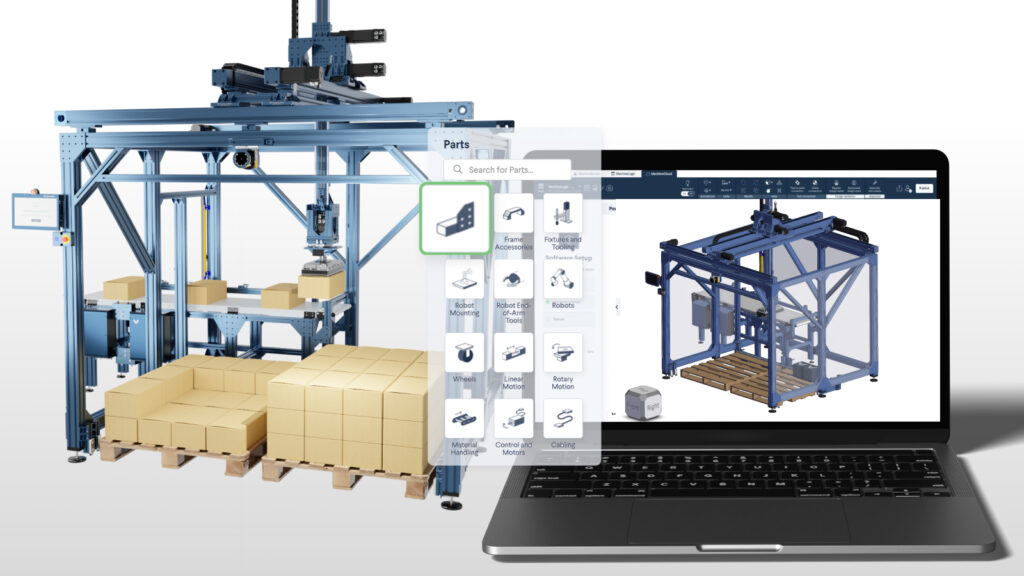
For the study, Vention evaluated the user behavior of its corporate customers on the Vention cloud platform MAP from January to December 2023. The aim was to capture the current state of DIY automation in companies and to explain how they use the DIY approach for the design, integration and operation of automation components, such as robot cells or cobot palletizers.
„The trend towards DIY automation continues this year,“ says Etienne Lacroix, CEO of Vention. „One driver is the shortage of skilled workers, which is becoming increasingly noticeable . The question of how production can be automated quickly and cost-effectively is currently occupying many companies. We see that small companies in particular are automating independently. But compared to last year, the number of large companies using DIY automation is increasing significantly.“
The most important findings of the study:
1. Small (< 200 employees (MA)) and medium-sized enterprises („Medium“, < 2,000 employees) were the leading users of automation systems on MAP in 2023, with a share of 48% and 17%, respectively. However, small businesses faced more challenging economic conditions in 2023. As a result, there was a decline of 12% in this segment compared to the previous year (see study, p. 8).
Large companies („Large“, < 10,000 employees) as well as the academic and government research sector („Academia & Gov Research“) have made significant gains in the use of the DIY approach on MAP (+10% and +4% respectively). Platform technology has made significant progress over the past year, providing more opportunities for high-throughput projects traditionally associated with larger manufacturers or users (see study, p. 8).
3. In 2023, very large companies („Enterprise“, > 10,000 employees) used the DIY approach more often in their factory floors than any other sector. Accordingly, the number of projects implemented with MAP in this segment has risen – from an average of 4.1 in 2022 to 4.9 projects in 2023 (see study, p. 11).
4. Projects with machine operation applications were the fastest implemented on MAP in 2023. This is likely due to the fact that it is difficult for companies to recruit staff given the ongoing labor shortages. As recent innovations have made CNC integration more accessible, manufacturers are more eager than ever to quickly adopt automated machine operation applications (see study, p. 24).
5. After two years of record sales (2021 and 2022), the Association for Advancing Automation (A3) reported a significant 30% decline in robot sales in North America in 2023. In contrast, robot deployments on MAP saw a notable increase in both 2022 and 2023. In 2023, robot deployments on MAP grew by about 40% (see study, p. 26).
The full study can be found here.