The Festo-MassRobotics Healthcare Robotics Startup Catalyst program celebrates the milestones achieved by the program’s four selected global startups at the Healthcare Robotics Engineering Forum. Key life sciences and robotics speakers to lead the event.
The successful Healthcare Robotics Startup Catalyst program came to an end on April 7th, 2022. The concluding ceremony will be held at the Healthcare Robotics Engineering Forum, Boston Convention and Exhibition Center, on May 11, 2022. The event includes an impressive line-up of speakers: Fady Saad, Co-founder & Vice President of Strategic Partnerships at MassRobotics; Alfons Riek, Vice President of Technology and Innovation at Festo; Kendalle Burlin O’Connell, President & Chief Operating Officer at MassBio; Kenn Turner, President and CEO at Mass Life Sciences Center; and Brian Johnson, President at MassMedic. All four selected startup companies, Kinarm (Canada), Assistive Technology Development Inc. (United States), Eureka Robotics (Singapore), and Bionomous (Switzerland ) will, in turn, promote their companies, along with their products and service offerings. They will also be demonstrating their technologies on the event’s expo floor.
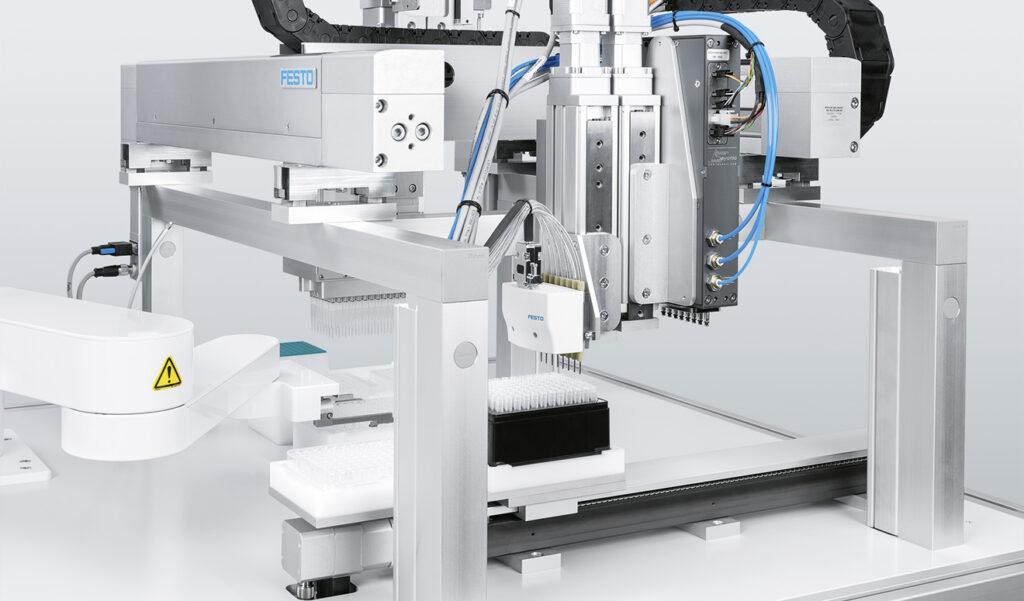
In October 2021, MassRobotics, Festo, and other key players in healthcare robotics, launched a Startup Catalyst Program to advance healthcare robotics companies around the world, by providing the networking opportunities, guidance, and resources they need to grow and succeed. The aim of the program was to connect healthcare robotics startups with customers, investors, suppliers, marketing, and overall support. The program focused on startups in the areas of clinical care, public safety, laboratory, supply chain automation, out-of-hospital care, quality of life, as well as continuity of work and education, and training and support for healthcare professionals.
More than 30 companies applied from all over the world, and the selection committee invited four to join in the program. The participating startups completed impressive milestones, as detailed below:
- Eureka Robotics develops and commercializes cutting-edge robotics and artificial intelligence (AI) technologies to automate high-accuracy, high-agility tasks. Eureka is currently completing fundraising rounds in Japan through connections provided by program mentors. Eureka was introduced to MassRobotics partner, Mitsubishi Electric, and signed a global partnership with Mitsubishi as a platinum partner. The program helped the company’s leadership to explore attractive applications in surgical lenses manufacturing technology, which is an extension to its focus on traditional manufacturing.
- Bionomous provides laboratory equipment to automate the screening, sorting, and pipetting of miniature biological entities for more ethical and faster research in life science. CEO Frank Bonnet reports that with the aid of the Catalyst Program, Bionomous was able to run a pilot program in the US, leading to the company’s first sales outside Europe. This convinced Bionomous to expand into the US market and set up offices in the MassRobotics space in Boston. Bonnet emphasized the importance of the program’s mentors, who connected them to key industry leaders to open possibilities for future partnerships.
- Assistive Technology Development Inc. is an American startup dedicated to at-home physical therapy solutions that are operable at a low cost and always accessible to rural patients and those who need closer monitoring for recovery. The company came into the program with three goals: 1) begin its first pilot study in a clinical setting; 2) downsize the actuation unit to a wearable form, and 3) raise capital. CEO Todd Roberts reports that with help from the program, the company has completed the first two milestones and is making progress on the third. It will begin phase I of a pilot study with UCHealth, a not-for-profit health care system, headquartered in Aurora, Colorado, on April 25th, allowing the company to present preliminary results at the keynote event at the Healthcare Conference. The study will assess the early clinical efficacy and collect patient and clinician feedback. Assistive’s actuation unit has been downsized by 70%, from a large, wall-powered, benchtop system to a wearable, battery-powered system that will enable the company to complete the pilot. Finally, Assistive is in the process of raising capital and has begun diligence with two firms.
- Kinarm uses robotic arms to provide an objective assessment method to identify, measure, and track cognitive motor or sensory impairments resulting from injury or disease. Kinarm worked with assigned mentors from the robotics ecosystem who provided introductions to industry leaders who responded with “jaw-dropping, you-can-do-that?” exclamations, reports Anne Vivian-Scott, CEO. Vivian-Scott was also introduced to experienced healthcare robotics leaders who will collaboratively aid Kinarm as the company scales its solutions. Vivian-Scott adds, “What we gained was not specific knowledge that can be encoded into our product, but direction. Quite frankly, most other programs are not ‘sufficiently vested’ in the participant’s business/opportunity to be able to offer such feedback.”
“I am grateful to Festo’s pioneering work to support our efforts to find global disrupting applications and startups in such a human-care field like healthcare, including life science, biotech, and medical devices,” said Fady Saad of MassRobotics.
“I am impressed with the quality of applications we received, and the unique structure of the program that allowed us to select such innovative companies and match them with world-class advisors,” said Festo’s Alfons Riek. “Certainly, we are excited about the networking opportunities opened to these companies and to presenting them to the world as great examples of the power of utilizing robotics in healthcare.”
MassRobotics, Festo, and additional corporations plan to launch the second version of the program by July 2022 to build on the programs’ amazing momentum and impact.
ABOUT MassRobotics: MassRobotics is the result of the collective work of a group of engineers, rocket scientists, and entrepreneurs with a shared vision to create an innovation hub and startup cluster focused on the needs of the robotics and IoT community. MassRobotics’ mission is to help create and scale the next generation of successful robotics and connected devices companies by providing entrepreneurs and innovative robotics/automation startups with the workspace and resources they need to develop, prototype, test, and commercialize their products and solutions. See www.massrobotics.org for details.
About Festo: Festo is a global player and an independent family-owned company with headquarters in Esslingen am Neckar, Germany. Festo has set standards in industrial automation technology and technical education ever since its establishment, thereby making a contribution to the sustainable development of the environment, the economy, and society. The company supplies pneumatic and electrical automation technology to 300,000 customers of factory and process automation in over 35 industries. The LifeTech sector with medical technology and laboratory automation is becoming increasingly important. The products and services are available in 176 countries. With about 20,000 employees in over 250 branch offices in 61 countries worldwide, Festo achieved a turnover of around €2.84 billion in 2020. Each year around 8 % of this turnover is invested in research and development. In this learning company, 1.5 % of turnover is invested in basic and further training. Festo Didactic SE is a leading provider of technical education and training and offers its customers worldwide comprehensive digital and physical learning solutions in the industrial environment.