Kostengünstige und leichte Plug&Play-Kombination aus Getriebe, Encoder, Controller, Kraftregelung und Motor für die Servicerobotik
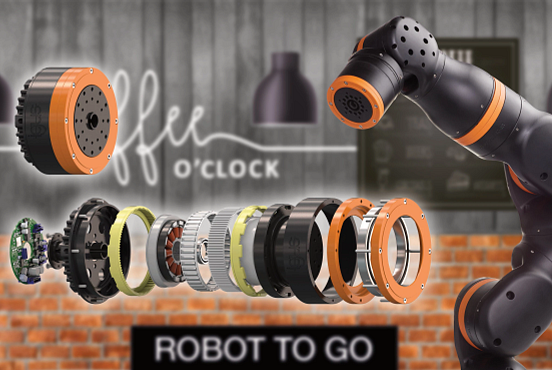
Köln, 3. Februar 2021 – Das Potenzial für die Servicerobotik ist enorm: In Küchen und Bars, in der Pflege, auf dem Acker oder in der Logistik helfen Leichtbauroboter, monotone oder nicht ergonomische Aufgaben zu automatisieren. Damit sich solche neuen Konzepte einfach und vor allem kostengünstig umsetzen lassen, stellt igus zur Hannover Messe einen neuen Getriebebaukasten für Cobots vor. Im Zentrum steht dabei das vollintegrierte Tribo-Wellgetriebe mit Motor, Absolutwert-Encoder, Kraftregelung und Controller.
„Wir befähigen Konstrukteure mit unseren Low-Cost-Automation-Lösungen kostengünstig in die Zukunft der Servicerobotik einzusteigen“, macht Stefan Niermann, in der erweiterten igus Geschäftsführung für den Bereich Low-Cost-Automation zuständig, deutlich. „Das eröffnet Raum für ganz neue Ideen im Bereich der Automatisierung: Roboter, die im Einzelhandel Kaffee ausschenken oder zuhause die Spülmaschine ausräumen können. Cobots, die in der Pflege eingesetzt werden, ebenso wie in der Industrie – und das alles made in Germany.“ Eine besonders wichtige Rolle spielen dabei die Getriebe, denn sie sind das Herzstück eines jeden modernen Roboters. Daher hat der motion plastics Spezialist igus im letzten Jahr eine neue Generation an Tribo-Wellgetrieben für die Bewegung an der 5. Roboterachse vorgestellt. Reibung und Verschleiß werden durch schmierfreie Tribo-Polymere optimiert. Der Einsatz von Kunststoffen ermöglicht eine äußerst kompakte Bauweise und eine kostengünstige Herstellung. Das drygear Wellgetriebe kann beispielsweise in der letzten Achse von Gelenkarm-, Portal- und Delta-Robotern vor verschiedenen Greifersystemen eingesetzt werden. Der neue Getriebebaukasten für Cobots, den igus auf der Hannover Messe 2021 zeigt, ergänzt nun das breite igus Angebot im Bereich der Low-Cost-Automation. Diese Plug&Play-Lösung hilft dabei, spannende Cobot-Ideen schnell in die Tat umzusetzen, ganz ohne sich Gedanken zur Leistungselektronik machen zu müssen.
Vollintegriertes Wellgetriebe für Low-Cost-Cobot-Anwendungen
Der Getriebebaukasten besteht aus Tribo-Wellgetrieben in den Größen 80 und 105 mit integriertem Motorcontroller, Kraftregelungselektronik, Absolutwert-Encoder und Motor. Im Getriebe kommen Tribo-Wellgenerator und Tribo-Flexring mit Außenverzahnung sowie ein Außenläufer Brushless DC Motor zum Einsatz. Auf Basis der Getriebe lässt sich mithilfe von Verbindungselementen ein individueller Roboter konstruieren, dank der zusätzlichen elektronischen Komponenten auch als Cobot. „Wir sehen für unsere leichten Kunststoff-Wellgetriebe Marktchancen in Robotern, die komplett unter 8kg wiegen“, stellt Alexander Mühlens, Leiter Low-Cost-Automation bei igus, heraus. „Denn bei der Robotik in der Low-Cost-Automation ist neben der Traglast und einem günstigen Preis immer auch das Eigengewicht wichtig. So lassen sich leichte Roboter einfacher transportieren und effizienter auf fahrerlose Transportsysteme, auf 7. Roboterachsen oder in naher Zukunft sogar an Drohnen einsetzen.“ Das geringe Gewicht ist auch beim Einsatz in Cobots ein deutlicher Pluspunkt, denn kleinere Massen bedeuten auch kleinere Kräfte bei Kollisionen. Dank der elektronischen Komponenten im vollintegrierten Wellgetriebe sind MRK-Fähigkeiten möglich. Mittels Absolutwert-Encoder-Technologie können Kräfte wie auch Momente über den Motorstrom ermittelt und sicher begrenzt werden. Dafür setzt igus auf einen Doppelencoder, bei dem eine Messung vor und hinter dem Gelenk erfolgt, um Kräfte und Drehmomente zu erkennen und darauf reagieren zu können.
igus Angebot im Bereich Low-Cost-Automation wächst kontinuierlich
Auch in einer neuen Version des igus Serviceroboters ReBeL sollen die neuen vollintegrierten Wellgetriebe in diesem Jahr zum Einsatz kommen. Diese Robotergeneration wird dadurch wesentlich schlanker und durch die integrierten BLDC-Motoren mit Leistungselektronik günstig. Alexander Mühlens stellt heraus: „Unser Ziel ist es, den ReBeL bereits ab geringen Stückzahlen für 2.900 Euro auf den Markt zu bringen. Er soll 2kg tragen können, eine Reichweite von bis zu 650 Millimetern besitzen, sowie ein Eigengewicht von unter 10kg und eine Mindestlaufzeit von 2 Millionen Zyklen.“ Der Cobot-Getriebebaukasten ergänzt das breite Portfolio von igus im Bereich der Low-Cost-Automation – von Getrieben über verschiedenste Roboterkinematiken bis hin zur Steuerung. Low-Cost-Automation bedeutet dabei sowohl kostengünstige Einstiegspreise als auch nur so viel zu automatisieren wie notwendig. Dadurch amortisiert sich die Investition innerhalb weniger Monate. Der neue Getriebebaukasten wird auch auf RBTX.com verfügbar sein. Auf dem Online-Marktplatz können sich Interessenten ihre Roboterkinematik mit Vision-, Safety- oder Greiferkomponenten so zusammenstellen, dass sie ihren Anforderungen und ihrem Budget genau entspricht. Dabei gilt das Versprechen, das alles zusammenpasst, sowohl auf Hardware- als auch auf Software-Seite – gemäß des igus Ansatzes „Build or Buy“, einen Roboter selbst zusammenstellen oder eine fertige Lösung erhalten.