BEIJING, Aug. 3, 2021 /PRNewswire/ — Luwu, a STEM education technology company, has announced the launch of XGO-Mini, a 12 DOF, omnidirectional quadruped robot that can interact with its surroundings using voice, image recognition, and tracking. This programmable, open-source robot is the perfect way to learn about robotics for new and advanced users. XGO-Mini is available now on Kickstarter: https://www.kickstarter.com/projects/xgorobot/xgo-mini-an-advanced-quadruped-robot-with-ai-modules.
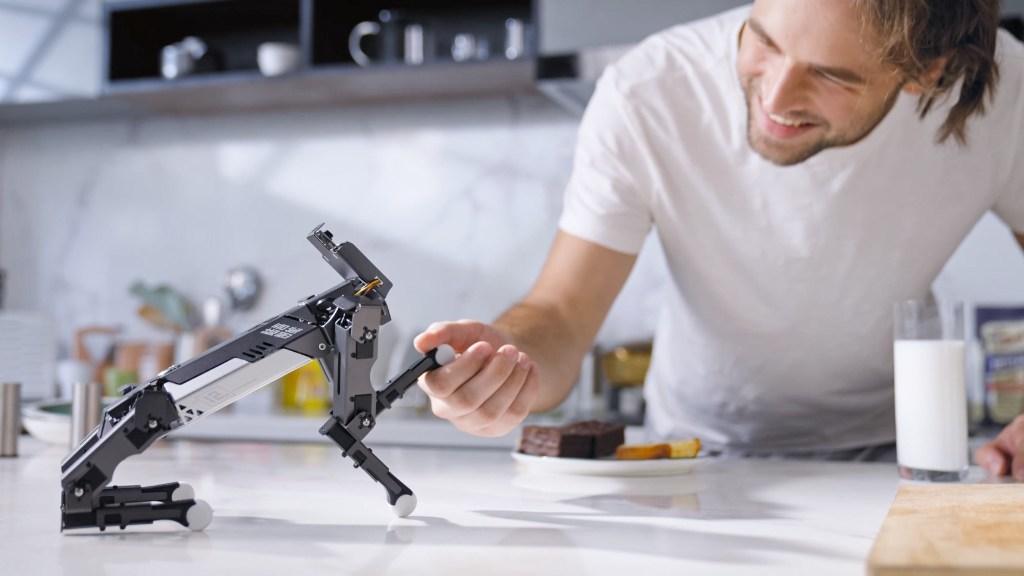
At first glance, XGO-Mini appears to be an incredible full-motion robotic dog. But it’s so much more than that. This desktop-sized AI quadruped robot with 12 degrees of freedom can achieve omnidirectional movement, six-dimensional posture and a variety of motions. As a quadruped robot, XGO-Mini can mimic the natural motion of a dog walking and is capable of movement on uneven terrain and extremely rough surfaces. It can even adapt to avoid obstacles by adjusting its height. With its unique bionic system, XGO Mini can perform any dynamic movement. Equipped with a 9-axis IMU, its joint position sensor and electric current sensor are able to reflect to its own posture and joint rotation angle and torque, which are used for algorithms verification and exploitation. The robot can be programmed for a variety of education, research, algorithm verification, and entertainment possibilities.
„As a technology company centered on robotics and STEM education, we understand the importance of robotics and AI education for youngsters. These technologies will be a key to the future. XGO Mini, a bionic quadruped robot dog for youth AI education, is the perfect platform for developing robotics and programming skills in a fun way. With 12 DOF, omnidirectional movement, and advanced-level AI, it is capable of virtually any movement or task and gives users unlimited programming possibilities that help users to explore, learn, and have fun,“ said Luwu Intelligence Technology Product Manager Pengfei Liu.
XGO-Mini is an incredibly versatile robot that can perform a variety of useful tasks and can be a very helpful assistant in daily life. It features fully functional AI modules that can facilitate both entry- and advanced-level AI applications. The Al modules feature visual recognition, voice recognition, and gesture recognition, giving XGO-Mini the ability to hear, recognize and reply to users like a real dog. It also can track multiple colors and recognize QR codes.
As an open-source robot with the Robot Operating System (ROS) and compatible with Python AI system, anyone can create their own functions for XGO-Mini. It can also be programmed by using common coding languages like Python and C++ that make it perfect for STEM education.
XGO-Mini Advanced Quadruped Robot with AI Modules is an incredible robotics platform for entertainment, STEM education, and exploring creativity. XGO-Mini is available now on Kickstarter with special pricing for early supporters. Learn more here: https://www.kickstarter.com/projects/xgorobot/xgo-mini-an-advanced-quadruped-robot-with-ai-modules.