4M KidzRobotix Fridge Robot
This robot can climb up your fridge
Revenues from Robotics Deployed in Warehouses to Cross US$51 Billion by 2030
Evolving e-commerce fulfillment operations and technical improvements in robotics tech and AI are rapidly growing the commercial robotics market
New York, New York – 18 Aug 2021, The warehousing industry has ramped up its automation efforts considering the increased order volume and labor shortages fueled by the pandemic. In addition to technology solutions such as Augmented Reality (AR) powered smart glasses and handheld devices with enhanced capabilities, autonomous, collaborative, and mobile robots are proving to be the most popular and fastest-growing productivity-enhancing solution in the warehouse workspace. According to ABI Research, a global tech market advisory firm, worldwide commercial robot revenue in warehouses will have a Compounded Annual Growth Rate (CAGR) of over 23% from 2021 to 2030 and exceed US$51 billion by 2030.
“Mobile robots are at the heart of the warehouse robotics market and account for most shipments and revenue. These robots, made up of Autonomous Guided Vehicles (AGVs) and Autonomous Mobile Robots (AMRs), are being used to move goods within the warehouse and being integrated within wider automated or manual workflows,” states Adhish Luitel, Industry Analyst, Supply Chain Management and Logistics at ABI Research.
Commercially speaking in the warehouse sector, robotics has moved from the early exploration phase to a more mature market in which early adopters are benefitting from live implementations of fully capable technical solutions. As a sign of the growing maturity of the market, a wide number of vendors such as Advantech, Brochesia, Kontakt.io, and RightHand Robotics now offer compelling products and solutions. The surrounding ecosystem of software vendors and systems integrators is also maturing, as software and integration capabilities become increasingly important factors for commercial differentiation. ABI Research has assessed fulfillment and warehousing processes of dominant operators such as Penske, A. Duie Pyle, Amazon, and JD.com to evaluate the efficacy of deploying solutions and friction points that might arise. These companies have been reaping the benefits of enhanced key performance metrics such as shorter dock-to-stock cycles and improved inventory accuracy thanks to successful deployment of various automation and vision-based solutions in their day-to-day operations.
“In addition to robots, warehouse operators should be seeking to combine the value of multiple solutions across the fulfillment workflow to achieve desired results. There is also a need for operators to look beyond productivity and assess how technologies affect worker satisfaction and safety, worker comfort, energy consumption, distance traveled, and error rates,” Luitel explains.
For example, “Pick-by-vision” solutions from augmented reality vendors such as Picavi demand a mere 15-minute training time and can boast up to 30% efficiency gains and up to 60% in time savings for training. In addition, order storage and automated order dispenser solutions from Alert Innovation help grocery retailers enhance their Return on Investment (ROI) by over 50% versus traditional automated picking systems.
“We can also expect intelligent automation solutions to influence processes across the supply chain. In the future, operators will be venturing further into solutions like Robotic Process Automation (RPA) and mobile warehousing,” Luitel concludes.
These findings are from ABI Research’s Modern Fulfillment Trends: Warehouse Robotics, Handheld Devices and Wearables technology analysis report. This report is part of the company’s Supply Chain Management & Logistics research service, which includes research, data, and ABI Insights. Based on extensive primary interviews, Application Analysis reports present in-depth analysis on key market trends and factors for a specific technology.
About ABI Research
ABI Research provides actionable research and strategic guidance to technology leaders, innovators, and decision makers around the world. Our research focuses on the transformative technologies that are dramatically reshaping industries, economies, and workforces today. ABI Research’s global team of analysts publish groundbreaking studies often years ahead of other technology advisory firms, empowering our clients to stay ahead of their markets and their competitors.
Mini RoboX-Adam Cardboard Robot
Luwu Intelligence Technology Announces Launch of XGO-Mini: An Advanced Quadruped Robot With AI Modules
BEIJING, Aug. 3, 2021 /PRNewswire/ — Luwu, a STEM education technology company, has announced the launch of XGO-Mini, a 12 DOF, omnidirectional quadruped robot that can interact with its surroundings using voice, image recognition, and tracking. This programmable, open-source robot is the perfect way to learn about robotics for new and advanced users. XGO-Mini is available now on Kickstarter: https://www.kickstarter.com/projects/xgorobot/xgo-mini-an-advanced-quadruped-robot-with-ai-modules.
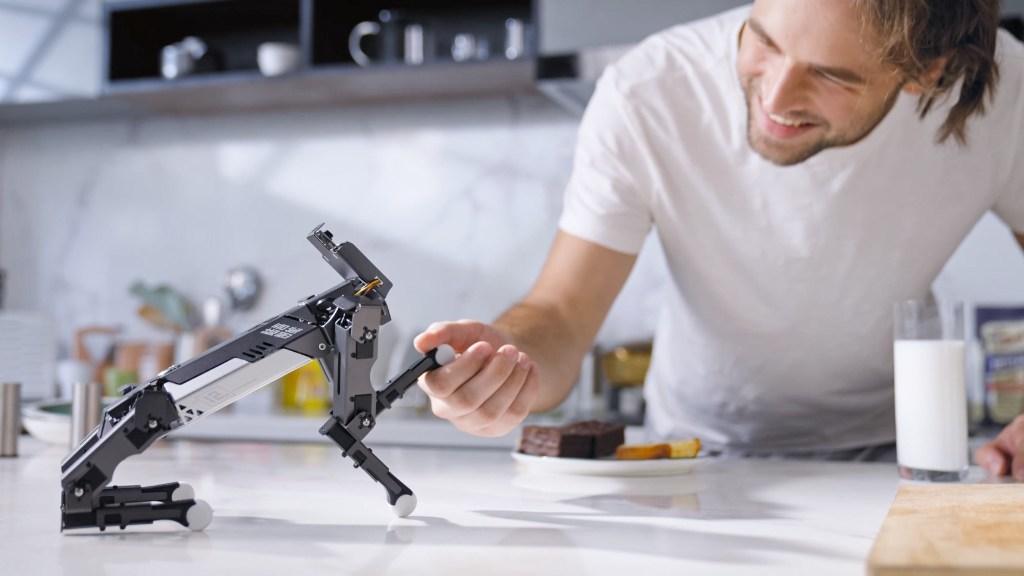
At first glance, XGO-Mini appears to be an incredible full-motion robotic dog. But it’s so much more than that. This desktop-sized AI quadruped robot with 12 degrees of freedom can achieve omnidirectional movement, six-dimensional posture and a variety of motions. As a quadruped robot, XGO-Mini can mimic the natural motion of a dog walking and is capable of movement on uneven terrain and extremely rough surfaces. It can even adapt to avoid obstacles by adjusting its height. With its unique bionic system, XGO Mini can perform any dynamic movement. Equipped with a 9-axis IMU, its joint position sensor and electric current sensor are able to reflect to its own posture and joint rotation angle and torque, which are used for algorithms verification and exploitation. The robot can be programmed for a variety of education, research, algorithm verification, and entertainment possibilities.
„As a technology company centered on robotics and STEM education, we understand the importance of robotics and AI education for youngsters. These technologies will be a key to the future. XGO Mini, a bionic quadruped robot dog for youth AI education, is the perfect platform for developing robotics and programming skills in a fun way. With 12 DOF, omnidirectional movement, and advanced-level AI, it is capable of virtually any movement or task and gives users unlimited programming possibilities that help users to explore, learn, and have fun,“ said Luwu Intelligence Technology Product Manager Pengfei Liu.
XGO-Mini is an incredibly versatile robot that can perform a variety of useful tasks and can be a very helpful assistant in daily life. It features fully functional AI modules that can facilitate both entry- and advanced-level AI applications. The Al modules feature visual recognition, voice recognition, and gesture recognition, giving XGO-Mini the ability to hear, recognize and reply to users like a real dog. It also can track multiple colors and recognize QR codes.
As an open-source robot with the Robot Operating System (ROS) and compatible with Python AI system, anyone can create their own functions for XGO-Mini. It can also be programmed by using common coding languages like Python and C++ that make it perfect for STEM education.
XGO-Mini Advanced Quadruped Robot with AI Modules is an incredible robotics platform for entertainment, STEM education, and exploring creativity. XGO-Mini is available now on Kickstarter with special pricing for early supporters. Learn more here: https://www.kickstarter.com/projects/xgorobot/xgo-mini-an-advanced-quadruped-robot-with-ai-modules.
4M KidzLabs Seifenblasen-Roboter
Dash Robotics/Mattel Kamigami Robots „Scarrax“ Scorpion
Dash Robotics/Mattel Kamigami Robots „Scarrax“. Find the latest News on robots drones AI robotic toys and gadgets at robots-blog.com. Follow us on our Blog Instagram Facebook Twitter or our other sites. Share your robotics ideas and products with us. #robots #robot #omgrobots #roboter #robotic #mycollection #collector #robotsblog #collection #botsofinstagram #bot #robotics #robotik #gadget #gadgets #toy #toys #drone #robotsofinstagram #instabots #photooftheday #picoftheday #followforfollow #instadaily #kamigami #origami #mattel #scorpion #insect #mattel #toyrobot
Sleepy Robot wants just 5 more minutes
When it’s too early in the morning and your robot refuses to work because it wants to snooze some more…
#igus #robolink #robot #robots #automation #lowcostautomation #snooze #morning #video #fun #sleep #just5moreminutes #tired #wakeup #robotsblog. Find the latest News on robots drones AI robotic toys and gadgets at robots-blog.com. Follow us on our Blog Instagram Facebook Twitter or our other sites. Share your robotics ideas and products with us. #robots #robot #omgrobots #roboter #robotic #mycollection #collector #robotsblog #collection #botsofinstagram #bot #robotics #robotik #gadget #gadgets