drylin XXL-Raumportalroboter ist bis zu 60 Prozent günstiger als vergleichbare Lösungen und besonders einfach in Betrieb zu nehmen
Köln, 8. Februar 2022 – igus erweitert sein breites Low-Cost-Automation Angebot um einen neuen drylin XXL-Raumportalroboter. Das Portal hat einen Aktionsradius von 2000 x 2000 x 1500 Millimeter und eignet sich besonders für Palettierungsanwendungen bis 10 Kilogramm. Der Roboter ist ab 7.000 Euro inklusive Steuerung erhältlich und lässt sich einfach selbst nach dem Do-it-yourself Prinzip aufbauen und programmieren – ohne Hilfe eines Systemintegrators.
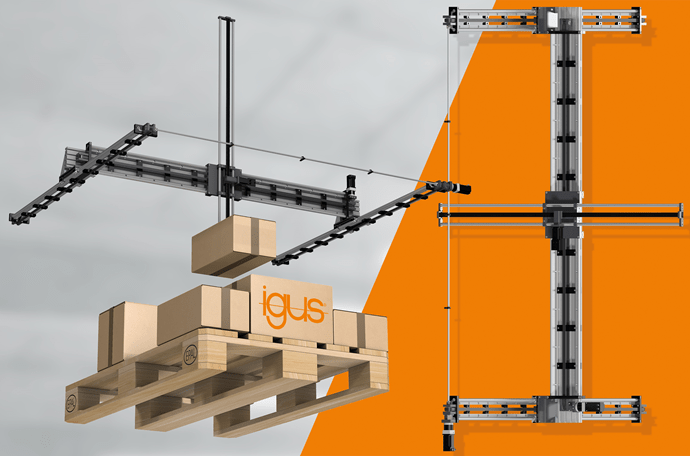
Zu teuer in der Anschaffung, zu aufwendig in der Programmierung, zu kompliziert in der Wartung: Viele kleine und mittelständische Unternehmen scheuen den Einstieg in die Automatisierung. Und gefährden damit langfristig ihre Wettbewerbsfähigkeit. Dabei geht der Einstieg ganz leicht von der Hand. Das beweist der drylin XXL-Portalroboter von igus. Der DIY-Bausatz bietet Unternehmen die Möglichkeit, schnell und unkompliziert einen Pick-and-Place Linearroboter für Aufgaben rund um Palettierung, Sortierung, Etikettierung und Qualitätsprüfung in Betrieb zu nehmen. „Palettier-Roboter, die in Zusammenarbeit mit externen Dienstleistern entstehen, kosten schnell zwischen 85.000 und 120.000 Euro. Das sprengt das Budget vieler kleiner Betriebe“, sagt Alexander Mühlens, Leiter Geschäftsbereich Low-Cost-Automation bei igus. „Wir haben deshalb eine Lösung entwickelt, die aufgrund des Einsatzes von Hochleistungskunststoffen und Leichtbaumaterialien wie Aluminium um ein Vielfaches günstiger ist. So kostet der drylin XXL-Raumportalroboter je nach Ausbaustufe zwischen 7.000 und 10.000 Euro. Eine Investition, die risikoarm ist und sich in der Regel innerhalb weniger Wochen amortisiert.“
DIY-Bausatz lässt sich ohne Vorkenntnisse schnell zusammensetzen
Das Raumportal erhält der Käufer als DIY-Bausatz. Bestandteile sind zwei Zahnriemenachsen und eine Zahnstangen-Auslegerachse mit Schrittmotoren und einem Aktionsraum von 2000 x 2000 x 1500 Millimeter. In der Maximallänge sind auch bis zu 6.000 x 6.000 x 1.500 Millimeter möglich. Zusätzlich ist im Paket ein Schaltschrank, Leitungen und Energieketten sowie die kostenlose Steuerungssoftware igus Robot Control (iRC) enthalten. Anwender können die Komponenten in wenigen Stunden zu einem betriebsfertigen Linearroboter zusammensetzen – ohne externe Hilfe, ohne Vorkenntnisse und ohne lange Einarbeitungszeit. Und werden noch zusätzliche Komponenten wie Kamerasysteme oder Greifer benötigt, so werden Anwender auf dem Robotik-Marktplatz RBTX schnell fündig.
Automatisierung entlastet Mitarbeiter
Zum Einsatz kommt der kartesische Roboter beispielsweise an Förderbändern, die Produkte von Spritzgussmaschinen abtransportieren. Hier nimmt der Roboter Artikel mit einem Maximalgewicht von 10 Kilogramm vom Band, transportiert sie mit einer Geschwindigkeit von bis zu 500 mm/s und positioniert sie mit einer Wiederholgenauigkeit von 0,8 Millimeter auf einer Palette. „Dank dieser Automatisierung können Betriebe ihre Mitarbeiter von körperlich anstrengenden und zeitaufwendigen Palettier-Aufgaben entlasten und Ressourcen für wichtigere Aufgaben gewinnen.“ Das System selbst verursacht dabei keinen Wartungsaufwand. Die Linearachsen bestehen aus korrosionsfreiem Aluminium, die Schlitten bewegen sich über Gleitlager aus Hochleistungskunststoff, die dank integrierter Festschmierstoffe über viele Jahre einen reibungsarmen Trockenlauf ohne externe Schmiermittel ermöglichen – selbst in staubigen und schmutzigen Umgebungen.
Digitaler Roboter 3D-Zwilling ermöglicht kinderleichte Programmierung
Doch nicht nur die Montage, sondern auch die Programmierung von Bewegungsabläufen stellt kein Einstiegshindernis dar. „Für viele Betriebe, die keine eigenen IT-Fachkräfte haben, ist die Programmierung von Robotern oft mit Problemen besetzt“, so Mühlens. „Wir haben deswegen mit der iRC eine kostenlose Software entwickelt, die optisch an häufig genutzte Office Software erinnert und eine intuitive Programmierung von Bewegungen ermöglicht. Das Besondere: die Software ist kostenlos und die so entstehende Low-Code-Programmierung kann dann 1:1 am realen Roboter verwendet werden.“ Herzstück der Software ist ein digitaler Zwilling des Raumportals, über den sich Bewegungen mit wenigen Klicks festlegen lassen. Auch im Vorfeld, bevor der Roboter in Betrieb ist. „Interessenten können vor dem Kauf anhand des 3D-Modells prüfen, ob gewünschte Bewegungen tatsächlich realisierbar sind. Zusätzlich laden wir alle Interessen ein, unsere Roboter live oder über das Internet kostenfrei auszuprobieren. Wir unterstützen sie bei der Inbetriebnahme und zeigen, was alles mit Low-Cost-Robotern möglich ist. Die Investition wird dadurch nahezu risikofrei.“