
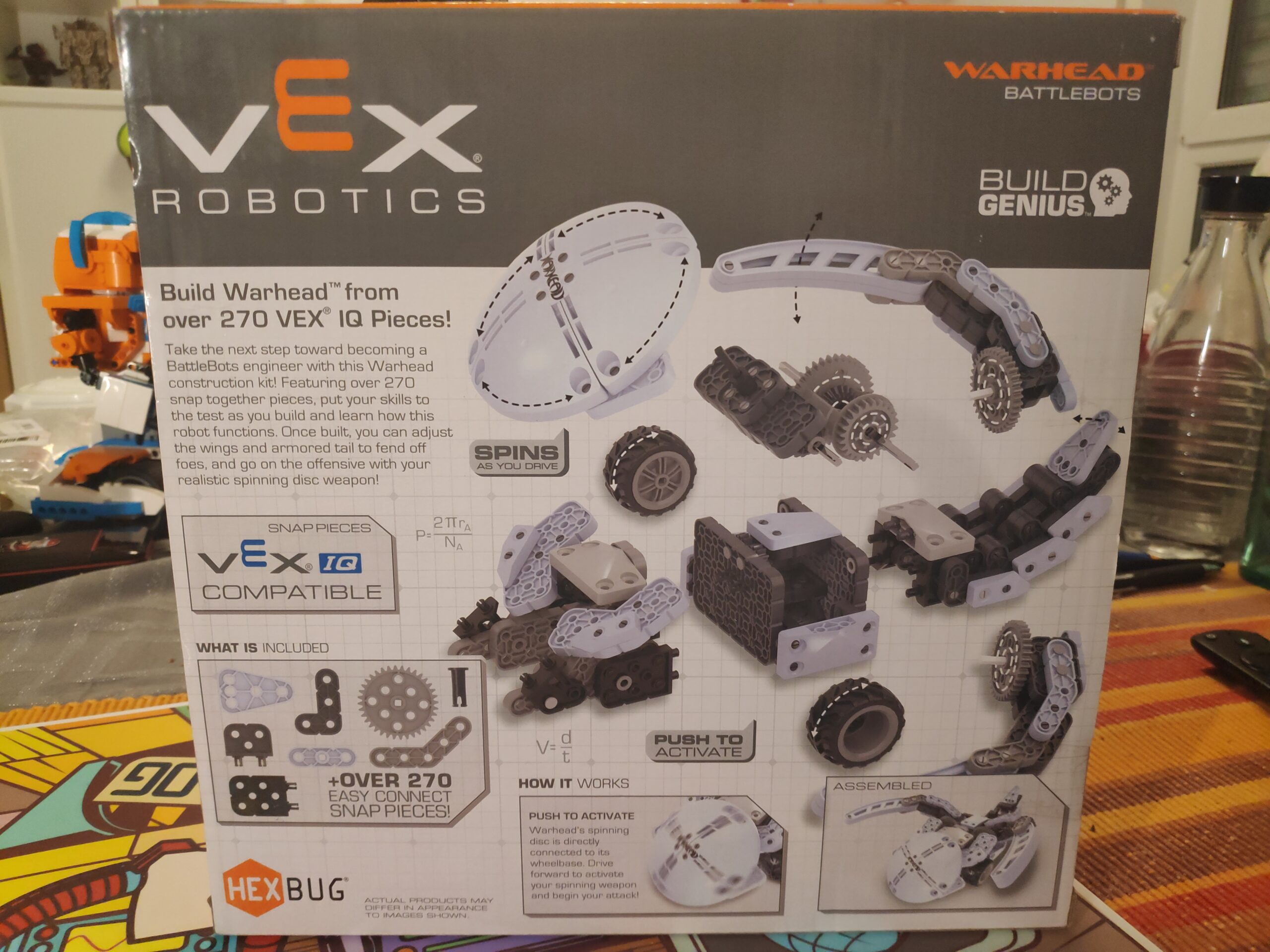
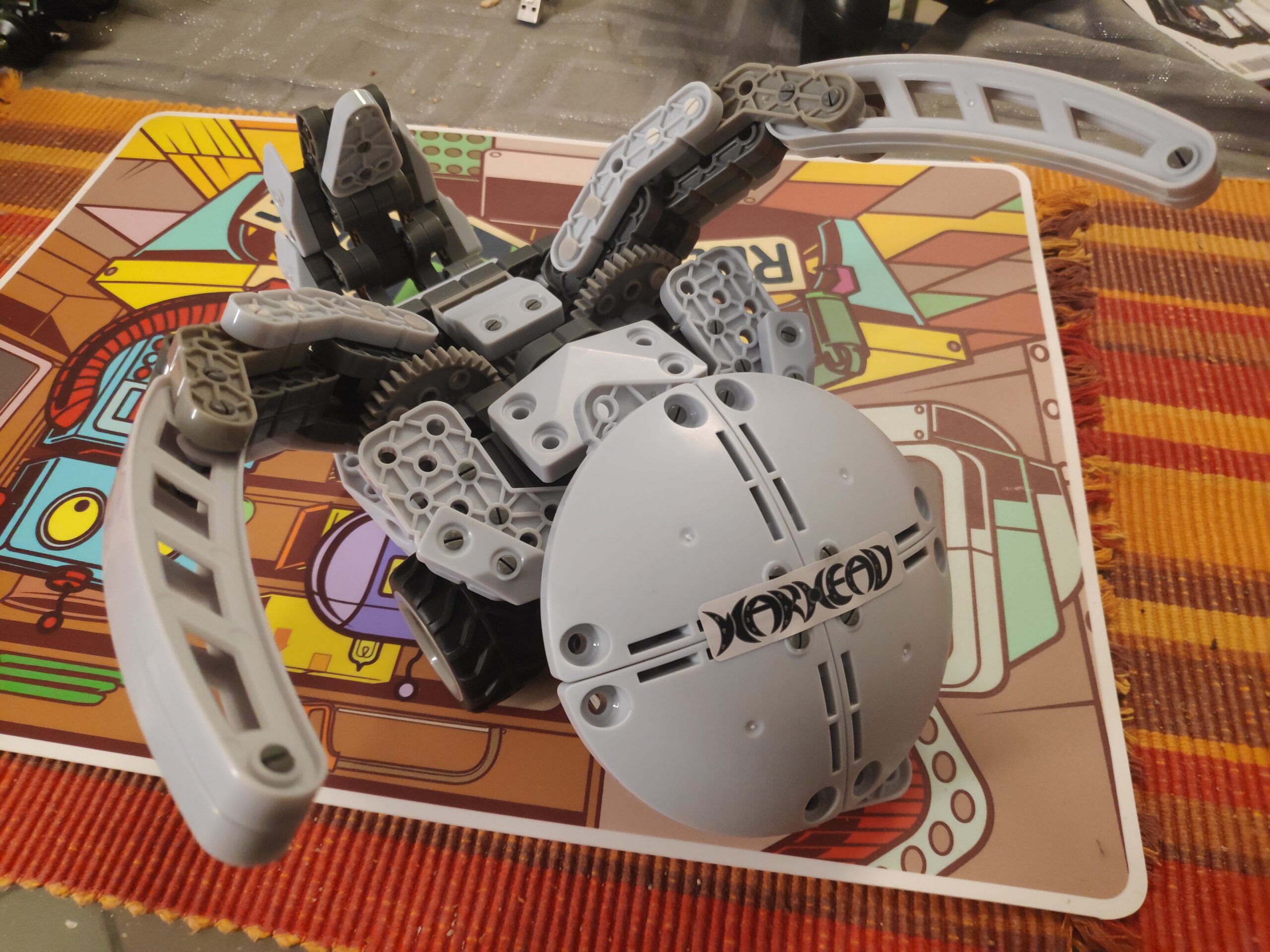
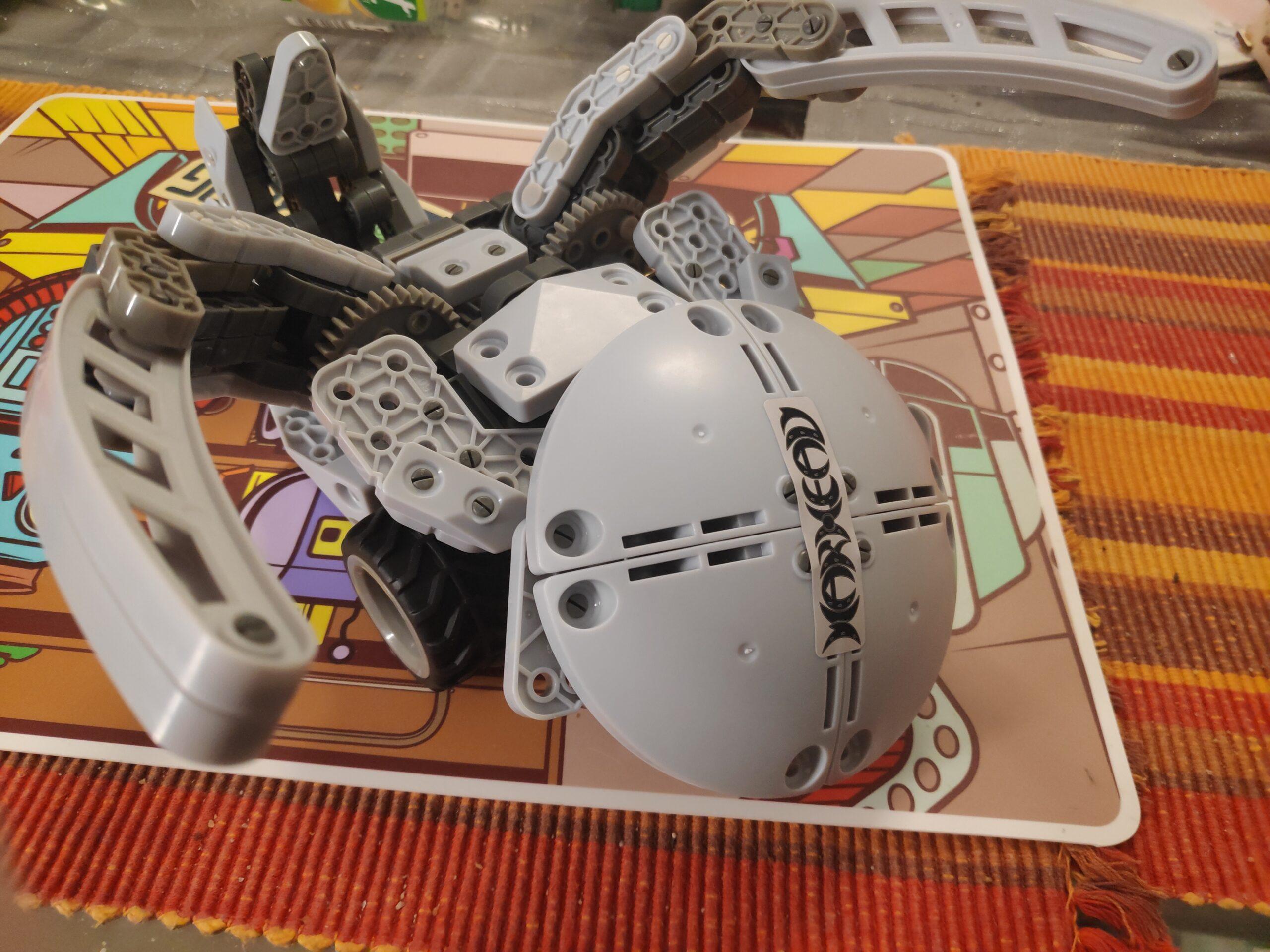
Ob Robotik, Elektronik oder klassische Techniken wie Mechanik, Statik und Pneumatik – fischertechnik bietet eine reiche Auswahl an Baukästen für Eltern, die ihren Kindern an Weihnachten ein Geschenk machen wollen, mit dem sie Spaß haben und etwas lernen können.
Weihnachten naht mit Riesenschritten und Viele sind auf der Suche nach einem Geschenk, mit dem sich Kinder und Jugendliche in der Weihnachtspause längere Zeit sinnvoll beschäftigen und vielleicht sogar etwas dabei lernen können.
Die aktuellen Baukästen von fischertechnik stehen mehr denn je für Spiel, Spaß und Lernen in einem. Dazu bieten die Sets die Möglichkeit, sich mit zukunftsweisenden Themen wie nachhaltige Energien und Robotics zu beschäftigen. Da ist zum Beispiel der fischertechnik Baukasten „Green Energy“, mit dem sich Kinder und Jugendliche ab 9 Jahren dem Thema erneuerbare Energien auf spielerische Art und Weise nähern. Sie können 14 spannende Modelle bauen und dabei lernen, wie die Gewinnung, Speicherung und Nutzung von Strom aus den natürlichen Energieträgern Wind, Wasser oder Sonne funktioniert.
Eine ideale Ergänzung zum Baukasten „Green Energy“ bietet der Bausatz H2 Fuel Cell Car. Hier wird spielerisch erkundet, wie eine Brennstoffzelle funktioniert und vor allem, wie die durch Wasserstoff gewonnene Energie genutzt werden kann. Die jungen Entdecker können mit dem selbst erzeugten Wasserstoff das Auto zum Leben erwecken und in Bewegung setzen.
Für Youngster ab 10 Jahren eignen sich die fischertechnik Baukästen Smarttech und Hightech. Die Jugendlichen können mit den Sets anspruchsvolle Programmieraufgaben lösen. Mit Omniwheels ausgestattete Roboter- und Fahrzeug-Modelle verdeutlichen die Funktionsweise des autonomen Fahrens und moderner mobiler Robotertechnik.
Spielspaß für Kinder ab 8 Jahren und die ganze Familie verspricht der Baukasten Funny Reactions, mit dem es fantasievoll, kreativ und temporeich zugeht. Mit 682 Bauteilen entstehen lustige und kreative Kettenreaktionen. Eine Seilbahn, ein Katapult und eine Abschusskanone sorgen für Tempo und Action.
Für Eltern, die ihre Kinder mit klassischen Techniken vertraut machen wollen, ist der Baukasten Retro Mechanics die ideale Wahl. Er veranschaulicht die Themen Mechanik und Statik anhand von 30 Modellen, die sich mit den im Kasten enthaltenen 500 Bauteilen konstruieren lassen. Das Retro-Design und die klassische Verpackung mit aufklappbarem Deckel sprechen auch die schenkenden Eltern an. Sämtliche Baukästen sind mit umfangreichem didaktischem Begleitmaterial ausgestattet, das auch online zur Verfügung steht.
Neben dem Ausprobieren der raffinierten Modelle können Kinder und Jugendliche auch eigene Konstruktionen entwerfen und drauf los bauen. Der Phantasie sind dabei kaum Grenzen gesetzt, denn die Bausteine sind äußerst stabil und erlauben auch meterhohe Konstruktionen. Weiterer Pluspunkt: Auch Papas und Mamas fischertechnik Sets können sich hier als nützlich erweisen. Denn seit der Markteinführung 1965 sind grundsätzlich alle Steine aus alten wie neuen Baukästen kompatibel.
Die hohe Qualität der fischertechnik Produkte ist wiederholt mit verschiedenen Auszeichnungen bedacht worden. Der Baukasten „Green Energy“ ist Kategoriesieger in der Rubrik „Spiel und Technik“ des Deutschen Spielzeugpreises 2021. Der Baukasten „H2 Fuel Cell Car“ ist „TOP 10 Spielzeug 2021“. Die „Top 10 Spielzeug“-Hitliste wird alljährlich vom Bundesverband des Spielwaren-Einzelhandels e.V. herausgegeben. Beide Baukästen sind darüber hinaus mit dem „spiel gut“-Siegel ausgezeichnet worden, einem der wichtigsten und renommiertesten Preise für gutes und pädagogisch wertvolles Spielzeug in Deutschland. Auch in Sachen Nachhaltigkeit sammelte fischertechnik Punkte: Zum zweiten Mal wurde das Unternehmen von Focus Money für sein nachhaltiges Engagement prämiert. Die Auszeichnung ist das Ergebnis von über 500.000 Bewertungen, die das Analyse- und Beratungshaus ServiceValue zusammen mit Focus Money zusammentrug.
Weitere Informationen unter www.fischertechnik.de
Auch wenn ich schon viele Roboter gebaut und getestet habe, ist dies heute eine Premiere! In den letzten Tagen habe ich zum ersten Mal einen Roboter von fischertechnik gebaut. Die Pressankündigung des fischertechnik Robotics Smarttech haben wir bereits in den letzten Tagen vorgestellt. [LINK]
Nun durfte ich ihn selber testen. Das Bausystem war mir zwar neu, hat mir aber auf Anhieb Spaß gemacht und ist wirklich einfach zu verwenden. Hat man sich einmal an die Bauanleitung und deren Stil gewöhnt, ist diese einfach verständlich. Während des Zusammenbaus des vierrädrigen Roboters mit den Omniwheels und dem Gestensensor, der mich ungefähr vier Stunden beschäftigt hat, habe ich dann auch gelernt auf welche Feinheiten ich in der Anleitung achten muss. Mir, als fischertechnik Neuling, sind zwei, drei Fehler passiert, die mir aber beim nächsten fischertechnik Modell bestimmt nicht mehr passieren würden. Überrascht war ich, dass man bei diesem Set die Kabel noch selber ablängen, abisolieren und die Steckverbinder anbringen muss. Das war ich aus anderem Roboter Kästen bisher nicht gewohnt; dies bietet aber die tolle Möglichkeit Kabel nach eigenen Wünschen und Längen zu erstellen. Diese Möglichkeit besteht bei vielen anderen Herstellern nicht und gerade wenn man mal einen etwas größeren Roboter baut, ist es von Vorteil wenn man lange Kabel selber fertigen kann.
Die Bauteile halten gut zusammen und es lassen sich sehr stabile Roboter konstruieren. Kinder brauchen hier vielleicht an der ein oder anderen Stelle etwas Unterstützung wenn die Teile, gerade wenn sie noch neu sind, noch etwas schwergängig zusammen zu stecken sind. Der von mir gebaute Roboter war dafür im Anschluss sehr stabil und überlebt selbst kleinere Stürze ohne dass Teile abfallen.
Die coolen Omniwheels ermöglichen es dem Roboter jederzeit in jede Richtung zu fahren. Solche Räder findet man in Robotersets leider viel zu selten! Daher fiel die erste Wahl auch direkt auf das Basismodell mit den neuen Omniwheels. Anschließend habe ich dies mit dem Spursensor und dem Gestensensor erweitert. Neben diesen beiden Modellvarianten sind Anleitungen für weitere sieben Roboter enthalten.
Der Roboter lässt sich entweder mit einem Netzteil oder mit einem Akku-Set betreiben, beides muss leider extra erworben werden.
Die aktuellste Version der für die Programmierung benötigten Software ROBOPro fand ich auf der Homepage von fischertechnik. Nachdem ich den Roboter über die Konfiguration auf dessen Touchscreen mit meinem WLAN verbunden habe (Okay: USB oder Bluetooth wäre auch gegangen, aber der Geek in mir musste direkt WLAN ausprobieren), konnte ich diesen mit der ROBOPro Software verbinden und programmieren. Das für die Cloud Funktionen benötigte Update wurde beim ersten Verbinden mit der ROBOPro Software mir sofort angeboten und ich konnte es problemlos installieren. Mit diesem Update lässt sich der Roboter als IoT Device in die fischertechnik Cloud einbinden und als smartes Gerät mit dem Internet kommunizieren. So kann man zum Beispiel eine Alarmanlage bauen, die einen über das Internet beim Auslösen alarmiert.
Neben der Möglichkeit in der ROBOPro Software grafisch zu programmieren, kann mit einer zusätzlichen frei verfügbaren Software auch in Scratch grafisch programmiert werden. Wer lieber textbasiert programmieren möchte kann dies auch in C. Da das Betriebssystem des Roboters auf Linux basiert, gibt es hier bestimmt noch jede Menge weitere, mir bisher unbekannte, Möglichkeiten den Roboter zu „hacken“ und noch mehr Funktionen hinzuzufügen. Das Einloggen auf dem Roboter per SSH ist auf jeden Fall möglich und über den SD-Karten Slot lassen sich alternative Betriebssysteme installieren und der Speicher erweitern.
Mein erster fischertechnik Roboter, genauer der Robotics Smarttech Roboter, hat mir bisher Freude bereitet und ich hatte Spaß daran mal ein mir bisher unbekannte Bausystem auszuprobieren. Mit den „selbstgebauten“ Kabeln und den universellen Ei- und Ausgängen am Controller, sowie der Cloud Anbindung, finden sich sicherlich auch tolle Einsatzmöglichkeiten abseits vom Einsatz als Spielzeugroboter.
Mit dem Baukasten Robotics Smarttech (249,90 Euro, erhältlich ab August) steigt fischertechnik in die nächste Dimension der fahrbaren Roboter ein. Mit neuen Bauteilen lassen sich verschiedene Omniwheels-Fahrzeuge konstruieren, die sich in sämtliche Richtungen bewegen können. Auch weitere Modelle, wie ein Tanzroboter, lassen sich mit dem Baukasten für Robotics-Einsteiger bauen und programmieren. Im Baukasten enthalten sind der TXT Controller und die Software ROBO Pro.
Der Baukasten Robotics Smarttech ermöglicht einen Einblick in die Zukunft autonom fahrender Fahrzeuge. Der enthaltene RGB-Gestensensor erkennt Gesten in vier verschiedenen Richtungen, misst RGB-Farbwerte und Umgebungshelligkeit, kann als Näherungssensor eingesetzt werden und misst hierbei Abstände von bis zu 15 Zentimetern. Zusammen mit dem IR-Spursensor und dem Taster lassen sich so verschiedene spannende Fahrroboter bauen und programmieren, die darauf warten, von jungen Tüftlern und Entwicklern auf Erkundungstour geschickt zu werden.
Die Fahrzeuge sind mit einem komplett neuen Räderkonzept ausgestattet, wie es in der mobilen Robotik vorkommt. Die Omniwheels – oder Allseitenräder – ermöglichen ein platzsparendes Rangieren, indem die Fahrzeige seitlich oder diagonal fahren. Außerdem können sich die Fahrzeuge sogar auf der Stelle drehen. fischertechnik entwickelte hierfür extra belastbare, qualitativ hochwertige Bauteile, um die Funktionalität der vielseitigen Fahrzeuge gewährleisten zu können.
Ein weiteres attraktives Modell ist der Tanzroboter, der – einmal zusammengebaut und programmiert – lustige Bewegungen und Drehungen vollziehen kann.
Bevor diese anspruchsvolleren Modelle gebaut werden, können sich Anfänger an einfachen Konstruktionen versuchen. Das Demo-Modell erklärt das Grundprinzip, wie Motor und Taster programmiert und gesteuert werden können. Per Knopfdruck läuft der Motor für eine zuvor definierte Zeit, währenddessen bewegt sich eine Drehschreibe mit einer Grafik, die eine optische Täuschung hervorruft. Erfahrene Konstrukteure wagen sich an einen fahrbaren Roboter, mit dem verschiedene Fahraufgaben programmiert werden können.
Insgesamt können mit dem Baukasten neun verschiedene Robotics-Modelle gebaut und programmiert werden. Der Baukasten ist für Kinder ab 10 Jahren geeignet.
VEX Robotics is revolutionizing workforce development education with VEX V5 Workcell
Sebastian from Robots-Blog was able to do a short interview with Annelie Harz from Wandelbots. Learn in the interview what Wandelbots is and why programming might soon become obsolete.
Robots-Blog: Who are you and what is your job at Wandelbots?
Annelie: My name is Annelie and I work as a marketing manager at Wandelbots.
Robots Blog: Which robot from science, movies or TV is your favorite?
Annelie: Wall-E, actually. A little robot that does good things and is just adorable.
Robots Blog: What is Wandelbots and where does the name come from?
Annelie: The name describes the CHANGE (german: „Wandel“) of RoBOTics. Because that is exactly what we do. We enable everyone to handle robots, which today is only reserved for a small circle of experts. Our long-term company vision is: „Every robot in every company and every home runs on Wandelbots“. And that promises big change on a wide variety of levels – starting for us with industry.
Robots Blog: Who is your product aimed at and what do I need for it?
Annelie: Our product is currently aimed at customers from industry. Here, our software – Wandelbots Teaching – can help with programming various applications such as welding or gluing without having to write a line of code. It is designed to be so simple and intuitive that really anyone can work with it to teach a robot a desired result. This works through the interaction of an app and an input device, the TracePen. This takes the form of a large pen with which users can draw a desired path for the robot on the component. But we also work together with educational institutions. They are the ones who train the next generation of robot experts. And in the long term, we are convinced – and this is already part of our vision – that robots will also find their way into private life as little helpers.
Robots-Blog: What feature is particularly worth mentioning?/What can’t anyone else do?
Annelie: Our product works robot manufacturer independent. In robotics, each manufacturer has developed its own proprietary programming language over the years. This makes communication between humans and machines very difficult. We, on the other hand, want to create a tool that allows any human to work with any robot – completely independent of programming language and manufacturer. Robotics should be fun for the user of our product. Thanks to the high usability and the operation of our app via iPad, this is already possible today. And over the next time, application-specific editions will be added to our platform – currently, for example, we are working on an app version for robot welding.
Robots Blog: Do I still need to learn programming at all?
Annelie: No. As I just explained, with this so-called no-code technology, you don’t need to learn programming anymore. It is simple, intuitive and user-friendly, even for laymen. Of course, you always need to have some basic understanding of robotics, especially for safety reasons. You should never underestimate the dangers posed by robots, which is why our product always works according to the respective manufacturer-specific safety specifications.
Robots Blog: What robots are supported? I have a Rotrics DexArm and an igus Robolink DP-5; can I use those as well?
Annelie: Of course, shortly after entering the market, we first want to make robotics in the industry, for example the automotive sector, more flexible and easier. To do this, we are gradually integrating the largest robot brands into our platform. We will certainly also integrate smaller robot brands that cover one or more niches. Or – even better – thanks to our Robot Integration Software Development Kit, robot manufacturers will soon be able to do it themselves.
Robots Blog: How much does your product cost?
Annelie: Our product is offered via a licensing model as a subscription, as is common in the Software as a Service business, or also classically for purchase. The current prices for the different editions can be found on our website (and you will certainly find more exciting content there)
The all-in-one smart toy incorporates science, technology, engineering and mathematics disciplines with playtime, in a hands-on way.
Astoria, New York – (May 3, 2021) Keeping children entertained and engaged in today’s tech-driven world is now easier with GinoBot. The tool that implements a fun, hands-on experiencewith unlimited expansion potential for learning STEM disciplines, computational thinking, and digital literacy is launching on Kickstarter today.
GinoBot seamlessly blends playtime with advanced learning to sharpen a child’s mind for the future. From plug-and-play robot to high-end coding and electronics, the progression of skills with GinoBot is unlimited. Children ages 6+ can build simple or complex models with GinoBot’s scalable, and compatible design.
It features KEIRO software for block-based programming, which is compatible with a PC (Windows, Linux, MAC OS) and smart devices (Google Play, Apple Store). GinoBot has Bluetooth and WiFi connectivity, as well as a micro USB connector. It can also connect with 3rd party hardware like Arduino, Microbit and Raspberry Pi, among others.
Science, technology, engineering and math, or STEM toys are the future. GinoBot is a solution for children to learn 21st century skills that lets them playfully learn how to code, design, build, and rebuild models quickly, no matter their age or learning style.
“Children are our future and we believe they are all gifted with the power to perform astonishing technological feats,” said Costas Sisamos, founder and CEO of Engino. “As STEM learning principles become more prominent in our children’s curriculum, GinoBot is a great learning tool that will keep young minds hungry to explore, design and create enabling them to experience the limitless thrill of scientific discovery.”
GinoBot is a great way to invest in your child’s imagination and expand their creativity. To pre-order, visit pr.go2.fund/ginobot.
About Engino
Engino is a toy manufacturer that specializes in construction toys and smart educational toys, and have been at the vanguard of the STEM education movement for the past 15 years. A few years ago, Engino joined the robotics market and started developing programmable robots. These robots are supported with an extensive curriculum so children can learn the digital-side of thinking and how to do programming, coding, and more. For more information, visit https://www.engino.com/.
WIXOM, MI, USA — Kawasaki Robotics’ dedication to continuous improvement is evident in their technically advanced general purpose robot line: the R series. With a history dating back to the mid-1980s, Kawasaki has continued to refine their general purpose robot arms over time, routinely producing robots with wider working ranges, faster cycle times, longer reach, and increased torque. The release of the RS007N/L models in 2017 marked the beginning of a new generation of Kawasaki R series and the latest model, the RS013N, is no exception. By offering a 13 kg payload capacity, a wide working range, small footprint and IP67-classi ed design, the NEW RS013N sets the industry benchmark for small-to-medium payload robots.
Industry Leading Speed & Flexibility
The new robot’s design includes a new arm structure, drive system and lighter main unit, which enables high speeds and a large working area. Its 1,460 mm reach is the largest in its class, allowing for installation flexibility and use in a wider variety of applications. The RS013N robot also leads its class in speed, resulting in reduced cycle times and increased productivity.
Introducing the easiest to use and most capable collaborative mobile manipulator for companies of all sizes.
NASHUA, NH, April 12, 2021 – Waypoint Robotics has teamed with Productive Robotics to make mobile manipulation accessible for small to mid-sized companies. Combine the easiest to use, most capable omnidirectional autonomous mobile robot with the simplest and most flexible 7 axis collaborative robot arm, and it has never been easier or more cost effective to deploy a mobile manipulator for manufacturing and logistics applications. Workers can use this mobile platform to perform repetitive tasks such as machine tending, quality assurance sampling, material replenishment, packaging, and many others, so they can focus on the high skilled jobs for which they are uniquely qualified.
“The fast and intuitive set up process of the Productive Robotics OB7 perfectly aligns with our Vector AMR that is built for factory and warehouse workers to deploy in minutes rather than hours or days,” said Waypoint Robotics CEO & Co-Founder Jason Walker. “And the extraordinary dexterity of Productive’s 7 axis cobot arm coupled with Waypoint’s omnidirectional mobility opens up endless possibilities for workers to automate repetitive tasks and maximize robot utilization throughout their facility, ”
What makes it so easy? Waypoint Robotics’ Vector AMR and Product Robotics’ OB7 have been elegantly integrated so set up and operation is fast, simple, and intuitive with both machines seamlessly working together as they perform tasks. The mobile manipulator has a flexible design and interconnected safety systems that allows for either robot to be the primary controller of a particular operation. The Vector’s omnidirectional mobility enables fast, precise docking in any direction or orientation so the OB7 can perform accurate and precise grasping or picking tasks, taking full advantage of the cobots’ 7 degrees of freedom (7 DOF) and superior dexterity. Power management is also a breeze because the Waypoint EnZone provides on demand energy and opportunity charging for longer run times.
“We have made cobots simple and more accessible for businesses, large and small, across all industries,” said Zac Bogart, President of Productive Robotics. “Working with Waypoint Robotics in developing this mobile manipulator platform will open the door for factories and warehouses to innovate, optimize productivity, and gain a competitive advantage with cobots.”
The ease of use, seamless integration, and cost-effective design of Waypoint Robotics’ Vector AMR and Productive Robotics’ 7 axis cobot, make this powerful autonomous mobile manipulator a real automation option for workers in businesses of all sizes. A mobile manipulator this accessible is an industry first.
About Waypoint Robotics
Waypoint Robotics, located in Nashua, NH, develops and manufactures fully autonomous, omnidirectional, mobile robots that are easy to use, industrial strength, and designed to be set up and used by the workforce that is on the job today. VectorTM , MAV3KTM and supporting products can be put to work immediately, adding to workers’ capabilities, increasing their efficiency, and strengthening their companies.
Factory Automation Systems joins Veo as its second Certified Systems Integrator
WALTHAM, MASS. (PRWEB) APRIL 06, 2021
Veo Robotics, Inc., an industrial automation company building technology to make robots responsive to humans, today announced that its flagship product FreeMove® has received safety certification from TÜV Rheinland for its industrial robot safeguarding system — making it a first-of-its-kind solution for human-robot collaboration. FreeMove is the only solution on the market today that implements dynamic, 3D Speed and Separation Monitoring and has been certified for compliance with ISO 13849 for PLd, Category 3. It is available for purchase now.
“This is a game-changer for human-robot interaction in industrial environments and a great accomplishment for the team,” said Veo Robotics CEO and Co-Founder Patrick Sobalvarro. “After spending the last four years visiting factories, working with our manufacturing customers, and building FreeMove, we are thrilled to be able to offer the fully safety-certified system.”
Additionally, Atlanta-based Factory Automation Systems (FAS) has joined Veo’s Certified Systems Integrator program. FAS is an industry veteran of nearly 30 years specializing in the creation of custom turnkey solutions. FAS will include FreeMove® as part of its safety solution offering to customers.
“Veo Robotics’ FreeMove is a first-of-its-kind safeguarding system that fills a need in the industrial robotics industry,” said Mark Ligler, VP of FAS. “We are excited to partner with Veo and offer FreeMove as part of our safety solution.”
FreeMove is available now. Please contact [email protected] to receive a quote for your workcell.
About Veo Robotics
Using advanced computer vision and 3D sensing, Veo Robotics is reinventing the way we manufacture products by giving standard industrial robots the ability to perceive and respond to their surroundings so they can work safely alongside humans. Veo provides the conditions for safe and dynamic interactions between humans and robots so that manufacturers can build more fluid, efficient, and flexible production lines. Veo currently partners with the four major robot manufacturers FANUC, Yaskawa, ABB, and Kuka. To learn more, visit http://www.veobot.com.