RBTX powered by igus treibt die Low Cost Automation weiter voran und erweitert sein Marktplatz-Angebot um UR Cobots
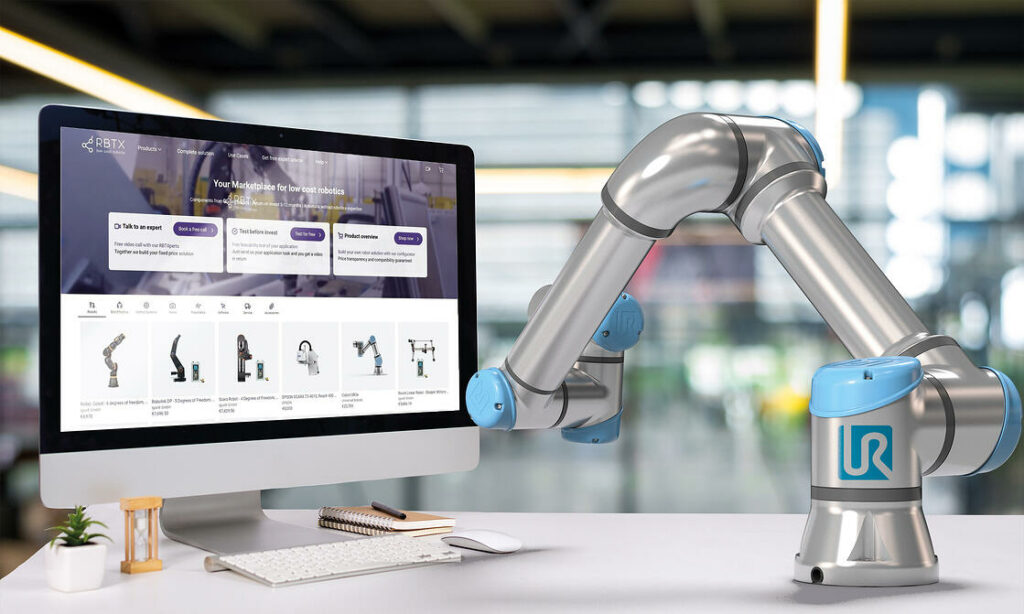
Köln, 4. Oktober 2022 – In der Industrie sind Roboter längst unverzichtbar. Doch insbesondere kleine und mittelständische Unternehmen stehen oftmals vor der Frage: Wie lässt sich eine Aufgabe mit wenig Aufwand kostengünstig automatisieren? Seit 2019 bietet der RBTX Marktplatz powered by igus, der Robotik-Anbieter und Anwender zusammenbringt, einfache und preiswerte Lösungen ab 2981 Euro – zum Beispiel einen Pipettierroboter mit allem Zubehör. Jetzt kooperiert RBTX auch mit Universal Robots, einem der Weltmarktführer für industrielle, kollaborierende Leichtbauroboter.
Flexible Automatisierungslösungen und eine schnelle Integration sowie intuitive Nutzung – dieses gemeinsame Ziel verfolgen der Marktplatz RBTX und der führende Cobot-Hersteller Universal Robots mit ihrem Robotik-Angebot. Um Synergien effektiv zu nutzen, verkündeten die beiden Unternehmen auf der Motek 2022 in Stuttgart nun den Start ihrer Partnerschaft in Deutschland, Österreich und der Schweiz im Rahmen des RBTX-Angebots des Kunststoff-Spezialisten igus. Über RBTX.com kooperiert der Marktplatz inzwischen mit 70 Unternehmen, die ihre Roboter, Greifsysteme, Kameratechnik, Förderbänder, Software und Services auf der Online-Plattform anbieten. Der Vorteil: RBTX gibt eine Kompatibilitätsgarantie für das gesamte Software- und Hardware-Angebot, sodass Anwender stets sicher gehen können, dass alle Komponenten miteinander funktionieren. „Mit Universal Robots haben wir nun einen weiteren namhaften Partner dazugewonnen, durch den wir das Produktangebot auf RBTX.com – abgesehen vom igus eigenen Roboter ReBeL – erstmals um Cobots erweitern können”, sagt Alexander Mühlens, Leiter Geschäftsbereich Automatisierungstechnik und Robotik bei igus. „Universal Robots ist nicht nur ein Pionier für Cobots, sondern auch wegweisend, wenn es um die intuitive Programmierung von Robotern geht. Das passt genau in das Konzept unseres Marktplatzes für Low Cost Automation-Lösungen, die sich auch ohne jegliche Vorkenntnisse schnell und unkompliziert umsetzen lassen. Daher freuen wir uns sehr, dass wir Universal Robots als Partner gewinnen konnten.“ Auf dem Marktplatz gibt es bereits zahlreiches Zubehör, wie die 7. Roboterachse von igus, welches sich mit den UR Cobots kombinieren lässt.
Gemeinsam Hürden senken
„Universal Robots bietet einfach zu integrierende Automatisierungslösungen, die es Kunden ermöglichen, ihre Wettbewerbsfähigkeit zu stärken und einen schnellen Return on Invest zu erzielen – das passt sehr gut zum Ansatz von RBTX”, sagt Andrea Alboni, General Manager Western Europe bei Universal Robots. Alexander Mühlens ergänzt: „Als offener Marktplatz sind wir immer an neuen Partnern interessiert, denn so können wir über unsere Plattform am Ende noch mehr individuelle Lösungen anbieten. Schließlich verfolgen wir ein gemeinsames Ziel: Automatisierung so zugänglich wie möglich zu machen.” Ganz nach dem „Build or Buy“-Prinzip finden Interessierte auf RBTX ein fertiges Robotik-System zum Festpreis oder können individuell Komponenten für die eigene Lösung zusammenstellen. Auf dem Marktplatz haben Interessierte auch jederzeit Zugang zum RBTXpert – einen Remote-Integrator-Service für Automatisierungslösungen mit Festpreis. Der RBTXperte prüft gemeinsam mit dem Kunden im Videochat (erste Stunde kostenfrei) die Machbarkeit der geplanten Anwendung und zeigt die Vorteile unterschiedlicher Kinematiken. Nach dem Beratungsgesprächs erhält der Kunde ein Angebot mit Festpreis – immer mit dem Fokus darauf, die kostengünstigste, funktionierende Lösung zu finden. Zudem hilft der RBTXpert bei der Inbetriebnahme. So findet auf RBTX.com jeder die passende Automatisierungslösung für seine Anwendung und sein Budget – auch ohne Automatisierungserfahrung oder Programmierkenntnisse. Dank des stetig wachsenden Partnernetzwerks bietet RBTX Kunden ein immer größeres Low Cost Automation-Universum – mit dem gemeinsamen Ziel, die Hürden in der Automatisierung weiter zu senken.