Researchers from Germany and Canada work on new AI methods for picking robots.
ISLANDIA, NY, July 7, 2021 — Production, warehouse, shipping – where goods are produced, stored, sorted or packed, picking also takes place. This means that several individual goods are removed from storage units such as boxes or cartons and reassembled. With the FLAIROP (Federated Learning for Robot Picking) project Festo and researchers from the Karlsruhe Institute of Technology (KIT), together with partners from Canada, want to make picking robots smarter using distributed AI methods. To do this, they are investigating how to use training data from multiple stations, from multiple plants, or even companies without requiring participants to hand over sensitive company data.
“We are investigating how the most versatile training data possible from multiple locations can be used to develop more robust and efficient solutions using artificial intelligence algorithms than with data from just one robot,“ says Jonathan Auberle from the Institute of Material Handling and Logistics (IFL) at KIT. In the process, items are further processed by autonomous robots at several picking stations by means of gripping and transferring. At the various stations, the robots are trained with very different articles. At the end, they should be able to grasp articles from other stations that they have not yet learned about. „Through the approach of federated learning, we balance data diversity and data security in an industrial environment,“ says the expert.
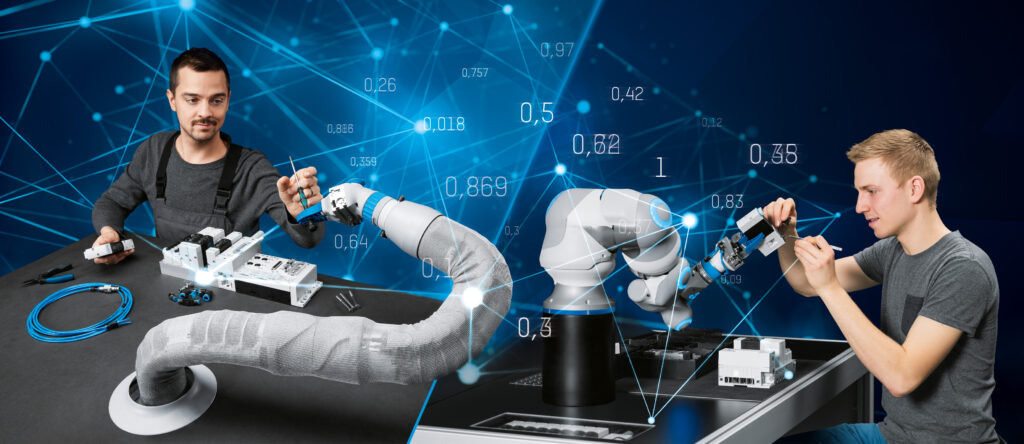
Powerful algorithms for industry and logistics 4.0
Until now, federated learning has been used predominantly in the medical sector for image analysis, where the protection of patient data is a particularly high priority. Consequently, there is no exchange of training data such as images or grasp points for training the artificial neural network. Only pieces of stored knowledge – the local weights of the neural network that tell how strongly one neuron is connected to another – are transferred to a central server. There, the weights from all stations are collected and optimized using various criteria. Then the improved version is played back to the local stations and the process repeats. The goal is to develop new, more powerful algorithms for the robust use of artificial intelligence for industry and Logistics 4.0 while complying with data protection guidelines.
“In the FLAIROP research project, we are developing new ways for robots to learn from each other without sharing sensitive data and company secrets. This brings two major benefits: we protect our customers‘ data, and we gain speed because the robots can take over many tasks more quickly. In this way, the collaborative robots can, for example, support production workers with repetitive, heavy, and tiring tasks”, explains Jan Seyler, Head of Advanced Develop. Analytics and Control at Festo SE & Co. KG During the project, a total of four autonomous picking stations will be set up for training the robots: Two at the KIT Institute for Material Handling and Logistics (IFL) and two at the Festo SE company based in Esslingen am Neckar.
Start-up DarwinAI and University of Waterloo from Canada are further partners
“DarwinAI is thrilled to provide our Explainable (XAI) platform to the FLAIROP project and pleased to work with such esteemed Canadian and German academic organizations and our industry partner, Festo. We hope that our XAI technology will enable high-value human-in-the-loop processes for this exciting project, which represents an important facet of our offering alongside our novel approach to Federated Learning. Having our roots in academic research, we are enthusiastic about this collaboration and the industrial benefits of our new approach for a range of manufacturing customers”, says Sheldon Fernandez, CEO, DarwinAI.
“The University of Waterloo is ecstatic to be working with Karlsruhe Institute of Technology and a global industrial automation leader like Festo to bring the next generation of trustworthy artificial intelligence to manufacturing. By harnessing DarwinAI’s Explainable AI (XAI) and Federated Learning, we can enable AI solutions to help support factory workers in their daily production tasks to maximize efficiency, productivity, and safety”, says Dr. Alexander Wong, Co-director of the Vision and Image Processing Research Group, University of Waterloo, and Chief Scientist at DarwinAI.
About FLAIROP
The FLAIROP (Federated Learning for Robot Picking) project is a partnership between Canadian and German organizations. The Canadian project partners focus on object recognition through Deep Learning, Explainable AI, and optimization, while the German partners contribute their expertise in robotics, autonomous grasping through Deep Learning, and data security.
- KIT-IFL: consortium leadership, development grasp determination, development automatic learning data generation.
- KIT-AIFB: Development of Federated Learning Framework
- Festo SE & Co. KG: development of picking stations, piloting in real warehouse logistics
- University of Waterloo (Canada): Development object recognition
- Darwin AI (Canada): Local and Global Network Optimization, Automated Generation of Network Structures
Visit www.festo.com/us for more information on Festo products and services.
About Festo
Festo is a leading manufacturer of pneumatic and electromechanical systems, components, and controls for process and industrial automation. For more than 40 years, Festo Corporation has continuously elevated the state of manufacturing with innovations and optimized motion control solutions that deliver higher performing, more profitable automated manufacturing and processing equipment.