Sebastian von Robots-Blog konnte ein kurzes Interview mit Annelie Harz von Wandelbots führen. Erfahrt im Interview was Wandelbots ist und warum demnächst vielleicht das Programmieren überflüssig wird.
Robots-Blog: Wer bist du und was ist deine Aufgabe bei Wandelbots?
Annelie: Mein Name ist Annelie und ich arbeite als Marketing Managerin bei Wandelbots.
Robots-Blog: Welcher Roboter aus Wissenschaft, Film oder Fernsehen ist dein Lieblingsroboter?
Annelie: Tatsächlich Wall-E. Ein kleiner Roboter, der Gutes tut und einfach nur liebenswert ist.
Robots-Blog: Was ist Wandelbots und woher kommt der Name?
Annelie: Der Name beschreibt den WANDEL der RoBOTik. Denn das ist genau das, was wir tun. Den Umgang mit Robotern, der heute nur einem kleinem Kreis von Experten vorbehalten ist, ermöglichen wir jedem. Unsere langfristige Firmenvision lautet: “Every robot in every company and every home runs on Wandelbots”. Und das verspricht einen großen Wandel in verschiedensten Ebenen – angefangen für uns bei der Industrie.
Robots-Blog: An wen richtet sich euer Produkt und was brauche ich dafür?
Annelie: Unser Produkt richtet sich derzeit an Kunden aus der Industrie. Hierbei kann unsere Software – Wandelbots Teaching – bei der Programmierung verschiedenster Applikationen wie z.B. Schweißen oder Kleben helfen ohne, dass man eine Zeile Code schreiben muss. Sie ist so einfach und intuitiv designed, dass wirklich jeder mit ihr arbeiten kann, um einem Roboter ein gewünschtes Ergebnis beizubringen. Dies funktioniert durch das Zusammenspiel einer App und eines Eingabegerätes, dem TracePen. Dieser hat die Form eines großen Stiftes, mit dem Nutzende dem Roboter am Bauteil beispielhaft einen gewünschten Pfad vorzeichnen können. Aber auch mit Bildungsträgern arbeiten wir zusammen. Sie sind es, die die nächste Generation von Roboterexperten ausbilden. Da darf unser Produkt natürlich nicht fehlen (Annelie grinst) Und langfristig sind wir – das steckt ja schon in unserer Vision – davon überzeugt, dass Roboter auch als kleine Helfer im Privatleben Einzug halten werden.
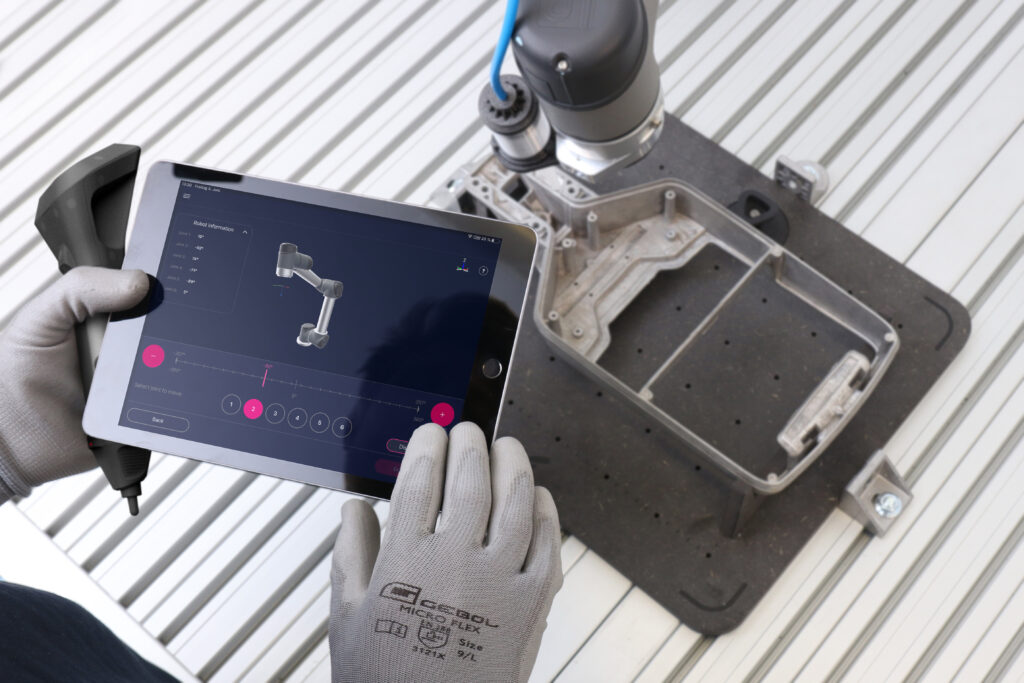
Robots-Blog: Welches Feature ist besonders erwähnenswert?/Was kann kein anderer?
Annelie: Unser Produkt arbeitet roboterhersteller-unabhängig. In der Robotik hat jeder Hersteller über die Jahre seine eigene proprietäre Programmiersprache entwickelt. Das macht die Kommunikation zwischen Mensch und Maschinen sehr schwierig. Wir wollen hingegen ein Tool schaffen, mit dem jeder Mensch mit jedem Roboter arbeiten kann – ganz unabhängig von Programmiersprache und Hersteller. Robotik soll dem Anwender unseres Produktes Spaß machen. Dank der hohen Usability und der Bedienung unserer App via iPad ist das heute schon möglich. Und über die nächste Zeit kommen applikationsspezifische Editionen in unsere Plattform – aktuell arbeiten wir beispielsweise an einer Appversion für das Roboterschweißen.
Robots-Blog: Muss ich dann überhaupt noch Programmieren lernen?
Annelie: Nein. Wie eben erklärt muss man mit dieser sogenannten No-Code Technologie nicht mehr programmieren lernen. Es ist einfach, intuitiv und nutzerfreundlich, selbst für Laien. Selbstverständlich muss man aber, vor allem aus Sicherheitsgründen, immer ein gewisses Grundverständnis über Robotik verfügen. Die Gefährdungen durch Roboter sollte man nie unterschätzen, deswegen arbeitet unser Produkt immer nach den jeweiligen herstellerspezifischen Sicherheitsvorgaben.
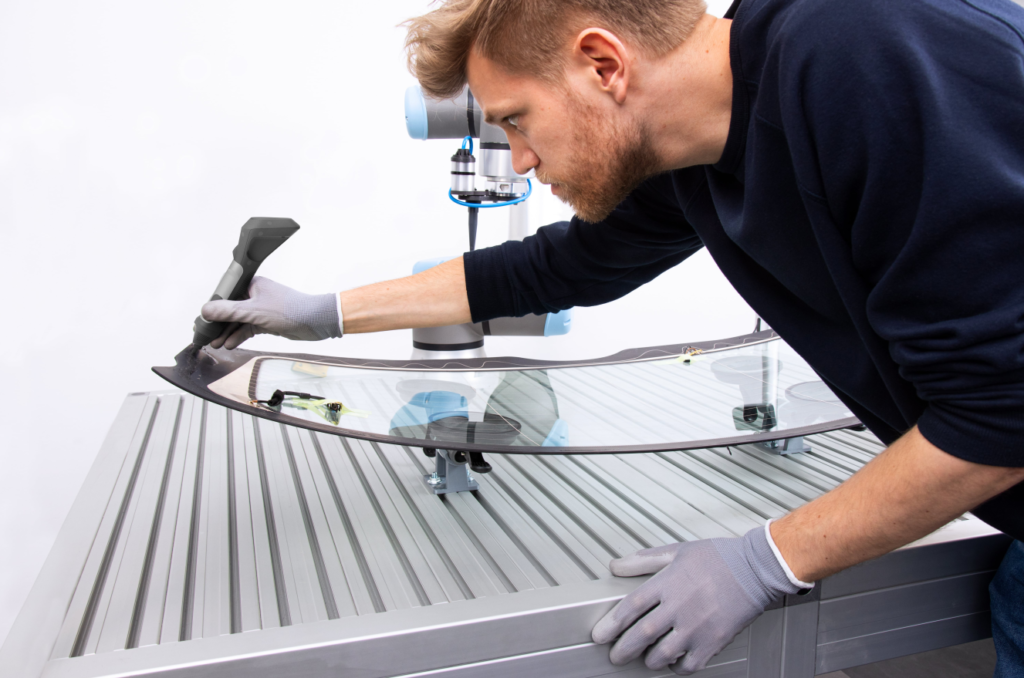
Robots-Blog: Welche Roboter werden unterstützt? Ich habe einen Rotrics DexArm und einen igus Robolink DP-5; kann ich diese auch verwenden?
Annelie: Wir wollen kurz nach dem Markteintritt natürlich erst einmal die Robotik in der Industrie, beispielsweise der Automobilbranche, flexibler und einfacher machen. Dafür integrieren wir die größten Robotermarken nach und nach in unsere Plattform. Kleinere Robotermarken, die eine oder mehrere Nischen abdecken, werden wir mit Sicherheit auch noch integrieren. Oder – noch besser – dank unseres Software Development Kits für die Roboterintegration können das Roboterhersteller demnächst sogar selbst.
Robots-Blog: Was kostet euer Produkt?
Annelie: Unser Produkt wird über ein Lizenzmodell als Subscription angeboten, wie es im Software as a Service Business üblich ist oder auch klassisch zum Kauf. Die aktuellen Preise für die unterschiedlichen Editionen könnt Ihr auf unserer Website finden (und dort bestimmt noch spannende weitere Inhalte finden)