Archiv der Kategorie: English
4M Green Science Rover Robot Hybrid Solar Power
4M KidzRobotix Motorised Robotic Arm
4M KidzRobotix Fridge Robot
This robot can climb up your fridge
Revenues from Robotics Deployed in Warehouses to Cross US$51 Billion by 2030
Evolving e-commerce fulfillment operations and technical improvements in robotics tech and AI are rapidly growing the commercial robotics market
New York, New York – 18 Aug 2021, The warehousing industry has ramped up its automation efforts considering the increased order volume and labor shortages fueled by the pandemic. In addition to technology solutions such as Augmented Reality (AR) powered smart glasses and handheld devices with enhanced capabilities, autonomous, collaborative, and mobile robots are proving to be the most popular and fastest-growing productivity-enhancing solution in the warehouse workspace. According to ABI Research, a global tech market advisory firm, worldwide commercial robot revenue in warehouses will have a Compounded Annual Growth Rate (CAGR) of over 23% from 2021 to 2030 and exceed US$51 billion by 2030.
“Mobile robots are at the heart of the warehouse robotics market and account for most shipments and revenue. These robots, made up of Autonomous Guided Vehicles (AGVs) and Autonomous Mobile Robots (AMRs), are being used to move goods within the warehouse and being integrated within wider automated or manual workflows,” states Adhish Luitel, Industry Analyst, Supply Chain Management and Logistics at ABI Research.
Commercially speaking in the warehouse sector, robotics has moved from the early exploration phase to a more mature market in which early adopters are benefitting from live implementations of fully capable technical solutions. As a sign of the growing maturity of the market, a wide number of vendors such as Advantech, Brochesia, Kontakt.io, and RightHand Robotics now offer compelling products and solutions. The surrounding ecosystem of software vendors and systems integrators is also maturing, as software and integration capabilities become increasingly important factors for commercial differentiation. ABI Research has assessed fulfillment and warehousing processes of dominant operators such as Penske, A. Duie Pyle, Amazon, and JD.com to evaluate the efficacy of deploying solutions and friction points that might arise. These companies have been reaping the benefits of enhanced key performance metrics such as shorter dock-to-stock cycles and improved inventory accuracy thanks to successful deployment of various automation and vision-based solutions in their day-to-day operations.
“In addition to robots, warehouse operators should be seeking to combine the value of multiple solutions across the fulfillment workflow to achieve desired results. There is also a need for operators to look beyond productivity and assess how technologies affect worker satisfaction and safety, worker comfort, energy consumption, distance traveled, and error rates,” Luitel explains.
For example, “Pick-by-vision” solutions from augmented reality vendors such as Picavi demand a mere 15-minute training time and can boast up to 30% efficiency gains and up to 60% in time savings for training. In addition, order storage and automated order dispenser solutions from Alert Innovation help grocery retailers enhance their Return on Investment (ROI) by over 50% versus traditional automated picking systems.
“We can also expect intelligent automation solutions to influence processes across the supply chain. In the future, operators will be venturing further into solutions like Robotic Process Automation (RPA) and mobile warehousing,” Luitel concludes.
These findings are from ABI Research’s Modern Fulfillment Trends: Warehouse Robotics, Handheld Devices and Wearables technology analysis report. This report is part of the company’s Supply Chain Management & Logistics research service, which includes research, data, and ABI Insights. Based on extensive primary interviews, Application Analysis reports present in-depth analysis on key market trends and factors for a specific technology.
About ABI Research
ABI Research provides actionable research and strategic guidance to technology leaders, innovators, and decision makers around the world. Our research focuses on the transformative technologies that are dramatically reshaping industries, economies, and workforces today. ABI Research’s global team of analysts publish groundbreaking studies often years ahead of other technology advisory firms, empowering our clients to stay ahead of their markets and their competitors.
Sleepy Robot wants just 5 more minutes
When it’s too early in the morning and your robot refuses to work because it wants to snooze some more…
#igus #robolink #robot #robots #automation #lowcostautomation #snooze #morning #video #fun #sleep #just5moreminutes #tired #wakeup #robotsblog. Find the latest News on robots drones AI robotic toys and gadgets at robots-blog.com. Follow us on our Blog Instagram Facebook Twitter or our other sites. Share your robotics ideas and products with us. #robots #robot #omgrobots #roboter #robotic #mycollection #collector #robotsblog #collection #botsofinstagram #bot #robotics #robotik #gadget #gadgets
SoftGripping expands its product line
SoftGripping, the internal robotic SoftGripper department of the logistic company Wegard GmbH has reached its market capitalization goal of 8 million Euro in the year 2020 and is now moving from the initial intent of establishing SoftGripping leadership in the cobot area towards the high-speed automation market. The internal project’s CTO and co-founder Alexey Stepanyuk is eager to tackle new areas with the industrial and hygienic line. “We focus on the needs of our customers and every development is custom to the application on hand” he emphasized in an interview, “our engineers know that solutions in food automation are as custom as the plants growing on the fields. There is a new evolutionary stage coming and we can’t wait to highlight it, although today’s robotics technology is far from perfect.” Let’s wait and see what the future brings!
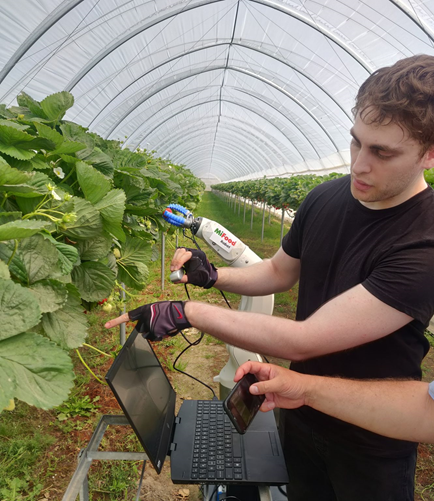
Information about hygienic line grippers: https://soft-gripping.com/hygienic-softgripper/
Information about industrial line grippers: https://soft-gripping.com/industrial-softgripper/
Igus Robolink RL-DP-5 Installation
Today I installed my new igus low cost Automation robotarm. This still counts as common computer peripheral, right? …Right?
Find the latest News on robots, drones, AI, robotic toys and gadgets at robots-blog.com. Follow us on our Blog, Instagram, Facebook, Twitter or our other sites. Share your robotics ideas and products with us. #robots #robot #omgrobots #roboter #robotic #mycollection #collector #robotsblog #collection #botsofinstagram #bot #robotics #robotik #gadget #gadgets #drone #robotsofinstagram #instabots #photooftheday #picoftheday #followforfollow #instadaily #werbung #igus #rbtx #lowcostautomation #robotarm #robolink #automation #showyourdesk
Better gripping with intelligent picking robots
Researchers from Germany and Canada work on new AI methods for picking robots.
ISLANDIA, NY, July 7, 2021 — Production, warehouse, shipping – where goods are produced, stored, sorted or packed, picking also takes place. This means that several individual goods are removed from storage units such as boxes or cartons and reassembled. With the FLAIROP (Federated Learning for Robot Picking) project Festo and researchers from the Karlsruhe Institute of Technology (KIT), together with partners from Canada, want to make picking robots smarter using distributed AI methods. To do this, they are investigating how to use training data from multiple stations, from multiple plants, or even companies without requiring participants to hand over sensitive company data.
“We are investigating how the most versatile training data possible from multiple locations can be used to develop more robust and efficient solutions using artificial intelligence algorithms than with data from just one robot,“ says Jonathan Auberle from the Institute of Material Handling and Logistics (IFL) at KIT. In the process, items are further processed by autonomous robots at several picking stations by means of gripping and transferring. At the various stations, the robots are trained with very different articles. At the end, they should be able to grasp articles from other stations that they have not yet learned about. „Through the approach of federated learning, we balance data diversity and data security in an industrial environment,“ says the expert.
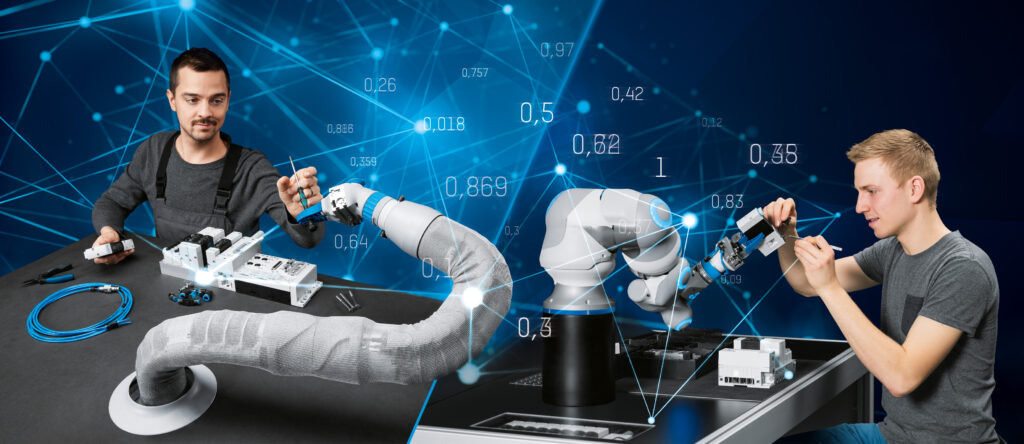
Powerful algorithms for industry and logistics 4.0
Until now, federated learning has been used predominantly in the medical sector for image analysis, where the protection of patient data is a particularly high priority. Consequently, there is no exchange of training data such as images or grasp points for training the artificial neural network. Only pieces of stored knowledge – the local weights of the neural network that tell how strongly one neuron is connected to another – are transferred to a central server. There, the weights from all stations are collected and optimized using various criteria. Then the improved version is played back to the local stations and the process repeats. The goal is to develop new, more powerful algorithms for the robust use of artificial intelligence for industry and Logistics 4.0 while complying with data protection guidelines.
“In the FLAIROP research project, we are developing new ways for robots to learn from each other without sharing sensitive data and company secrets. This brings two major benefits: we protect our customers‘ data, and we gain speed because the robots can take over many tasks more quickly. In this way, the collaborative robots can, for example, support production workers with repetitive, heavy, and tiring tasks”, explains Jan Seyler, Head of Advanced Develop. Analytics and Control at Festo SE & Co. KG During the project, a total of four autonomous picking stations will be set up for training the robots: Two at the KIT Institute for Material Handling and Logistics (IFL) and two at the Festo SE company based in Esslingen am Neckar.
Start-up DarwinAI and University of Waterloo from Canada are further partners
“DarwinAI is thrilled to provide our Explainable (XAI) platform to the FLAIROP project and pleased to work with such esteemed Canadian and German academic organizations and our industry partner, Festo. We hope that our XAI technology will enable high-value human-in-the-loop processes for this exciting project, which represents an important facet of our offering alongside our novel approach to Federated Learning. Having our roots in academic research, we are enthusiastic about this collaboration and the industrial benefits of our new approach for a range of manufacturing customers”, says Sheldon Fernandez, CEO, DarwinAI.
“The University of Waterloo is ecstatic to be working with Karlsruhe Institute of Technology and a global industrial automation leader like Festo to bring the next generation of trustworthy artificial intelligence to manufacturing. By harnessing DarwinAI’s Explainable AI (XAI) and Federated Learning, we can enable AI solutions to help support factory workers in their daily production tasks to maximize efficiency, productivity, and safety”, says Dr. Alexander Wong, Co-director of the Vision and Image Processing Research Group, University of Waterloo, and Chief Scientist at DarwinAI.
About FLAIROP
The FLAIROP (Federated Learning for Robot Picking) project is a partnership between Canadian and German organizations. The Canadian project partners focus on object recognition through Deep Learning, Explainable AI, and optimization, while the German partners contribute their expertise in robotics, autonomous grasping through Deep Learning, and data security.
- KIT-IFL: consortium leadership, development grasp determination, development automatic learning data generation.
- KIT-AIFB: Development of Federated Learning Framework
- Festo SE & Co. KG: development of picking stations, piloting in real warehouse logistics
- University of Waterloo (Canada): Development object recognition
- Darwin AI (Canada): Local and Global Network Optimization, Automated Generation of Network Structures
Visit www.festo.com/us for more information on Festo products and services.
About Festo
Festo is a leading manufacturer of pneumatic and electromechanical systems, components, and controls for process and industrial automation. For more than 40 years, Festo Corporation has continuously elevated the state of manufacturing with innovations and optimized motion control solutions that deliver higher performing, more profitable automated manufacturing and processing equipment.
BeBot, the beach cleaning robot, is the first in the Searial Cleaners product line
If you need a beach cleaner, just ask for BeBot from The Searial Cleaners range. This robot cleans beaches to meet an essential environmental need and drastically simplifies the daily chore. Poralu Marine has developed a product that is perfectly adapted to its clients’ business concerns.
Not only does BeBot help protect the environment, but it does so without polluting: it is the only fully electric beach cleaner on the market, using both batteries and solar panels. It therefore emits no greenhouse gases.

Thanks to its technology, widely acclaimed by the scientific community, it protects fauna buried under the sand, notably turtle eggs. It helps prevent beach erosion and does not weaken beach subsoils.
To fine clean the sand, the cleaner robot is steered by remote control, which helps protect both the user and the environment. This silent multi-purpose robot can pull loads of up to 1000 kg or be fitted with a trailer to transport parasols, deckchairs, and so on. Both easy to use and autonomous, the robot greatly facilitates the work of its users.
BeBot is very quiet and can move around cleaning all day on the beach without disturbing tourists, boaters and people working on the beach.
As part of a framework agreement with the Italian company Niteko, Poralu Marine manufactures, markets and distributes this product throughout the world via a well-established network of partners on every continent.